Get Help With Your Project Today
Want to know if we can help with your project or want more information about our engineering design & assessment services? Leave your contact details below and we'll be in touch to discuss your requirements.
Get In Touch
DOCAN HEAD OFFICE (UK) DOCAN USA OFFICEDOCAN Engineering Design & Assessment Consultancy
The core services that we provide include CAE involving systems, process, structural mechanics, thermo-fluids, engineering design, CAD, drafting, FEA & CFD, classical analysis, and both design code and fitness for service assessments.
Concept & Prototype
development
You might have an idea but not necessarily the high level engineering resource to develop the idea to a prototype – this is where DOCAN can help. We work with clients across a range of industries providing services from concepting to prototype generation through to assessment of prototype designs and creation of manufacturing drawings. We can facilitate manufacture of parts with the aid of our manufacturing partners, both for traditional methods of manufacture, such as machining and fabrication, and for Additive Manufacturing (AM), which is particularly useful for rapid prototyping.
We can help you present concept material for funding applications, produce engineering calculations to verify your concept and work for you to turn your idea into a feasible design with drawings for you to conduct prototype testing.
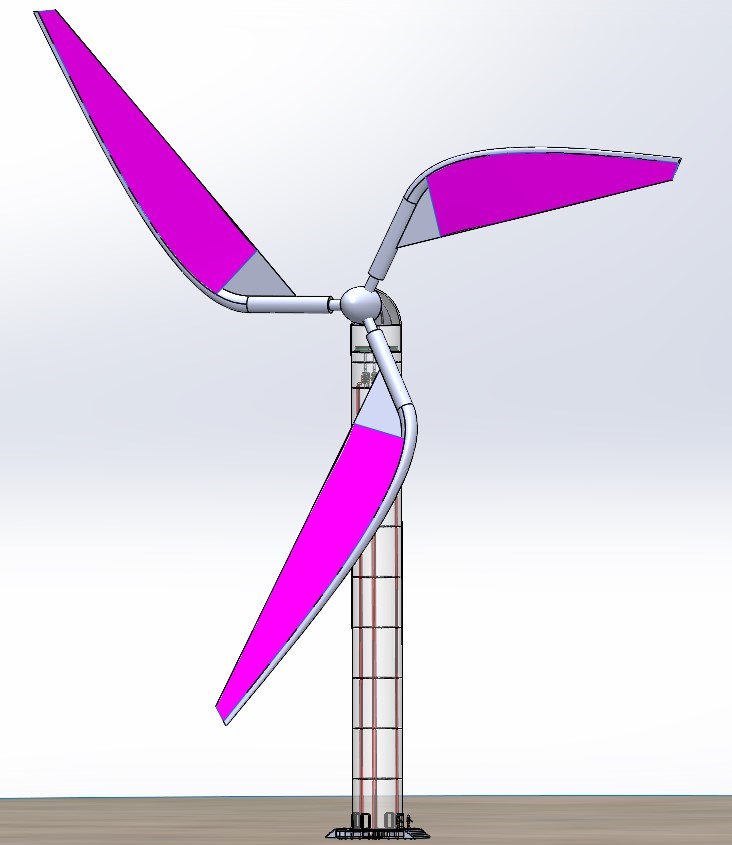
Project Management
Services
We work with our clients to ensure that projects are run in a controlled environment and following methodologies (i.e. PRINCEII, PMP, etc.), to deliver on time, on budget, and using controlled resources. This allows our clients to put their own high level engineering resource where it is needed and be confident that their projects are running smoothly.

Designing from
first principles
DOCAN have design expertise to assist with design concepting, optioneering, FEED, detailed design, machining, fabrication and more. We can then facilitate creation of construction drawing, O&M manuals and any product documentation which may be required.
We regularly work to international design codes such as ASME, BSI, API, DNV, etc. to deliver code compliant designs.
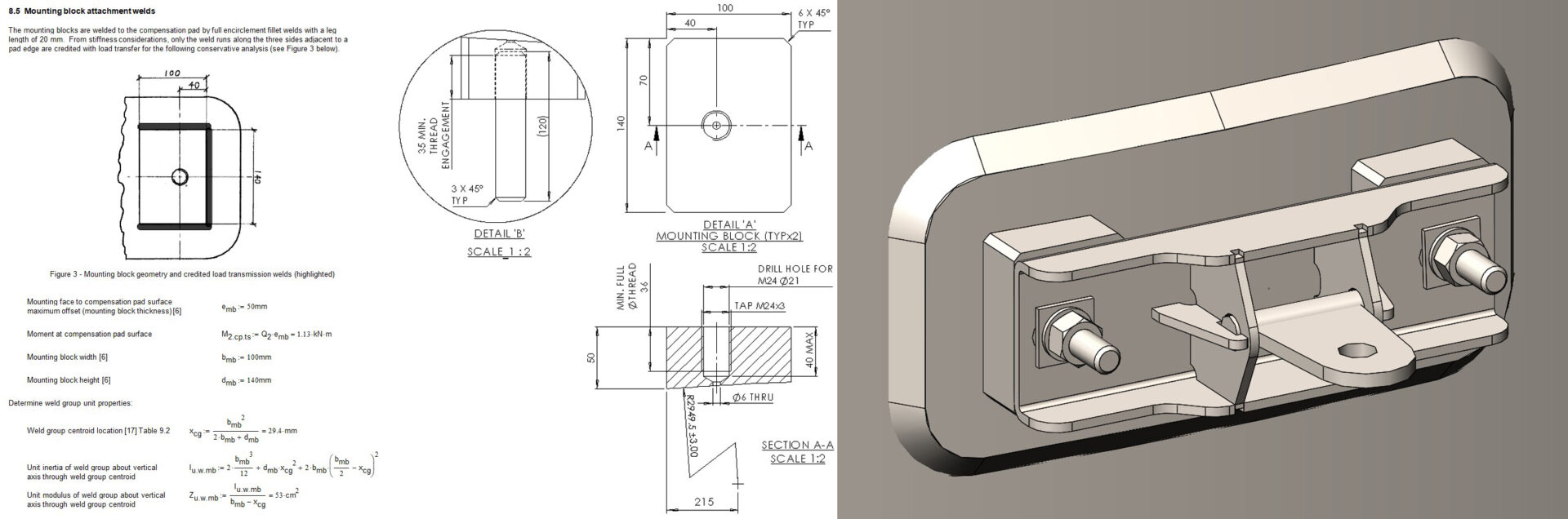
Design with Simulation
One of our key differentiators to our competitors is how we use design and analysis to offer a better engineered solution, being stronger, lighter, cheaper, or whatever the client requires. Our expertise can assist you in solving problems in the fields of structures, fluid dynamics, thermo-fluids, process, and chemical engineering.
Typical applications we have worked on cover designing to increase available margins against design code requirements, modifying client designs to pass design code requirements, determining Cv curves for valves, determining loading due to pipe slug flow and designing suitable pipe supports among many more.
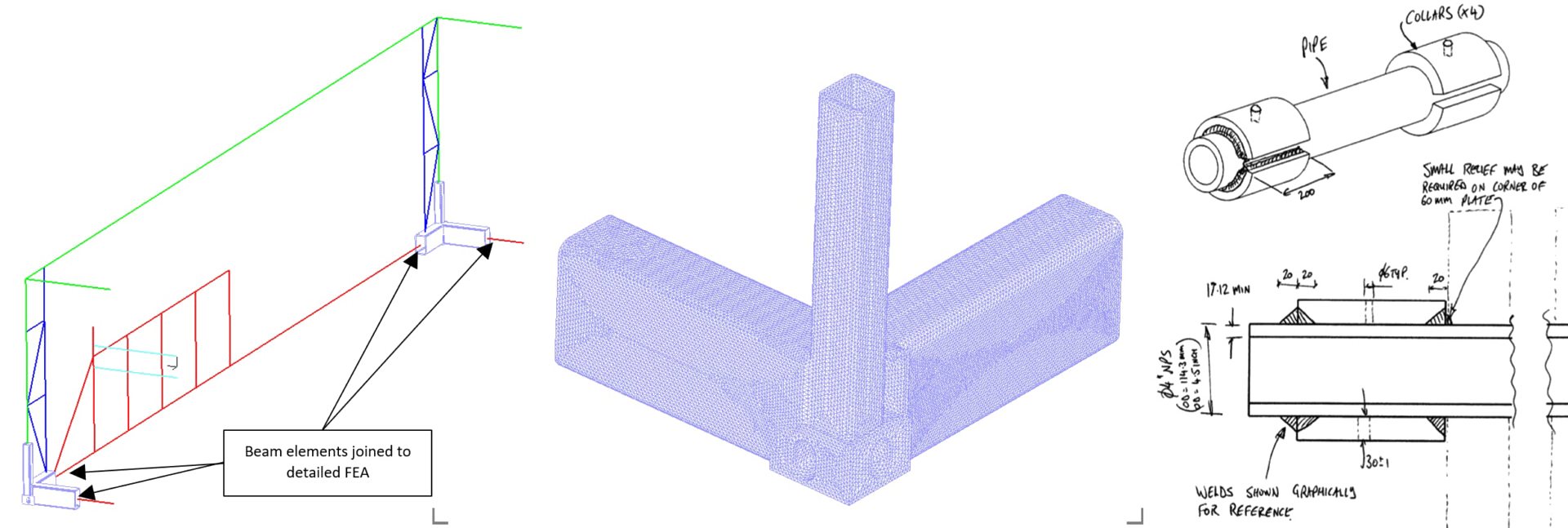
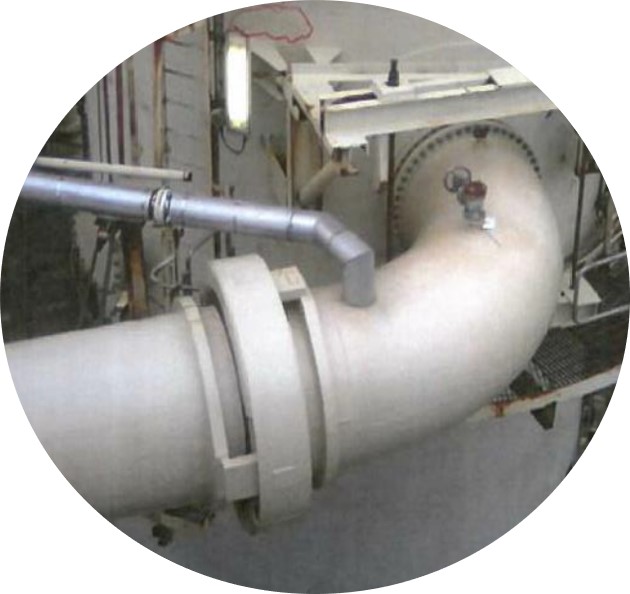
FFS and Integrity Assessment
Over time we have undertaken many Fitness-For-Service and Integrity assessment projects for our clients, from single code checks to complex multiphysics level 3 analyses resulting in continuous operation, re-rates, repair designs, decommissioning & lift-out or shutdowns. One example was for a UK client to assess a corroded section on a tank near to a pipe support. As no design information was available for the pipe work, which included several bellows joints, we combined hand calcs, pipe stress analysis methods, pressure vessel design software and FEA to provide a solution to the client.
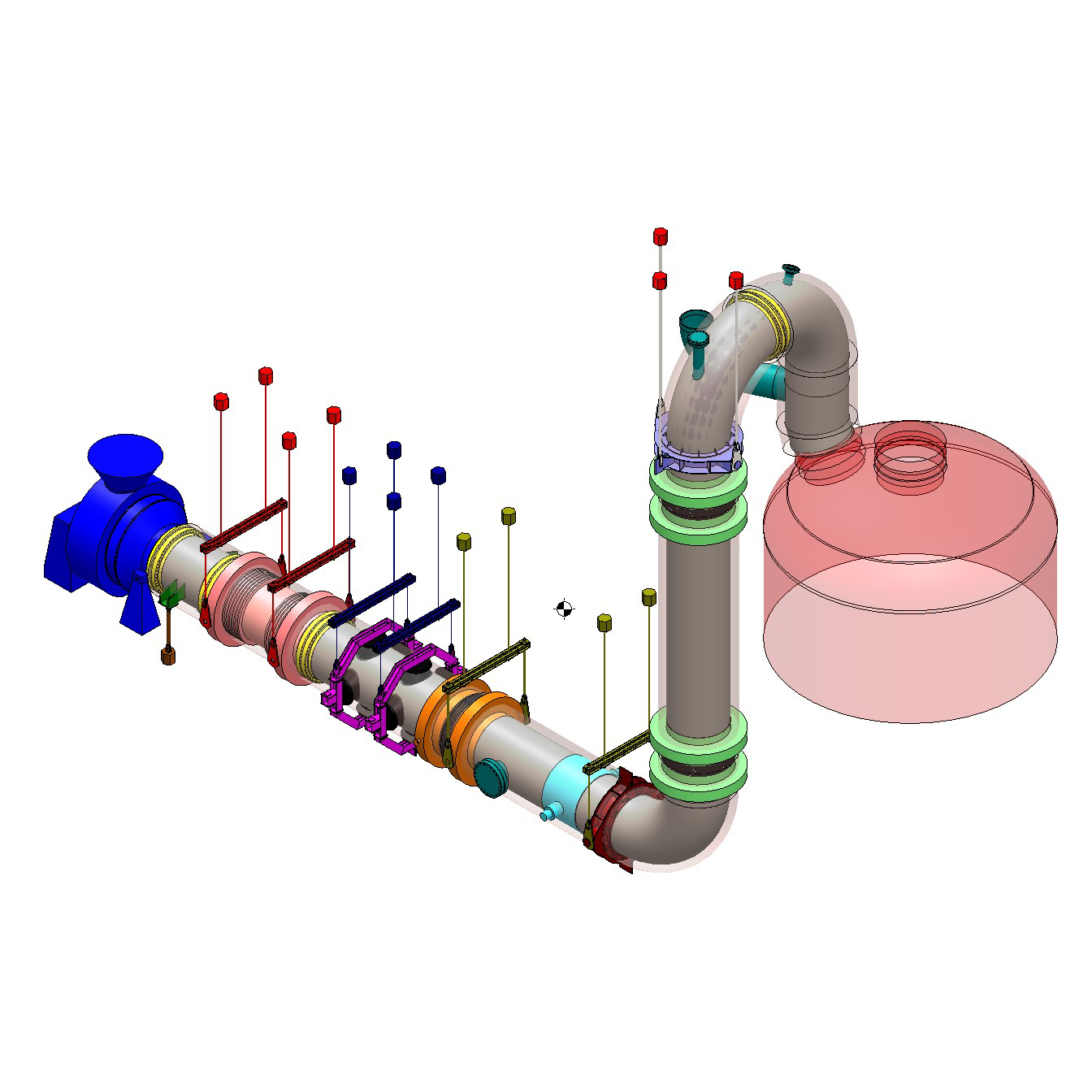
Failure Assessment & Re-design
As well as understanding how to design, we also have the expertise to work out why things fail. One of these cases was for a UK oil refinery, where a very hot (+700°C) and large diameter (60” OD) pipeline within the creep range had bottomed out on it’s spring hanger supports. We assessed the line, determined the cause of failure, assessed the effects on connected equipment and then re-specified the hangers along with providing new stress isometrics for the line.
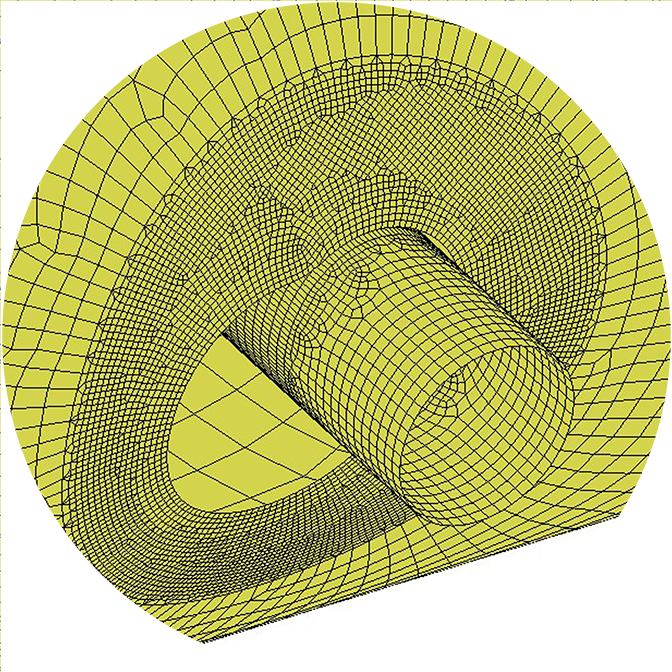
Decommissioning studies
A great example of this work was for DOCAN to verify the structural integrity of three pressure vessels which were to be lifted out for decommissioning. The heaviest vessel was 455Te, 50m long and Ø5m. Our scope included design of the lifting interface, manual calculations to the Eurocode lifting standards and verification using non-linear elastic-plastic FEA methods. Our verification principles ensure that we never use simulation as just a ‘black box’ and always work to justify our results with multiple methods. The vessel was lifted over a live plan area, so safety of the lift was imperative. Within the assessment work, studies were used to ensure that damaged equipment was still safe to lift and included modification of the vessel to make the safe to lift.