Consultancy
FFS Assessments
DOCAN have a wealth of experience conducting comprehensive Fitness for Service (FFS) assessments to assess the current and future integrity of a range of assets.
DOCAN's FFS Assessment Capabilities
We have vast expertise working within pressure systems engineering, serving our clients to guide and verify the defect tolerance or fitness for service of their systems.
We can perform FFS assessments to a variety of codes including API 579, BS 7910 and EDF R6.
We have undertaken many Fitness for Service assessment projects for our clients, from single code checks to complex multi-physics analyses resulting in continuous operation, re-rates, repair designs, decommissioning & lift-out, or shutdowns.
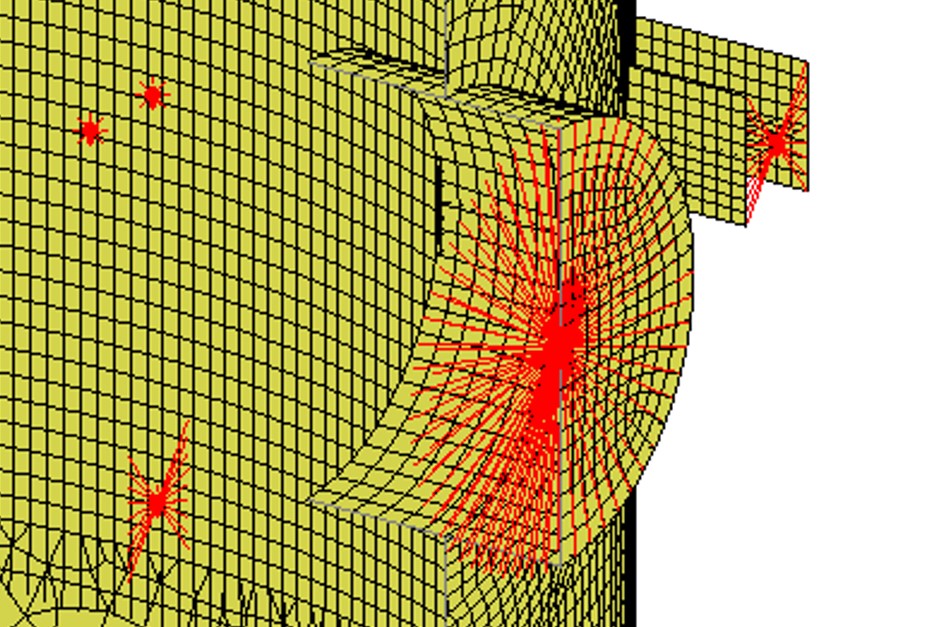
We employ a range of solutions, including manual calculations and simulation & analysis to accurately perform detailed assessments of equipment such as:
- Piping systems (process piping, water/steam/gas etc)
- Pressure systems (pressure vessels, tanks, valves, pipes, heat exchangers, etc)
- Welded structures
- Turbines
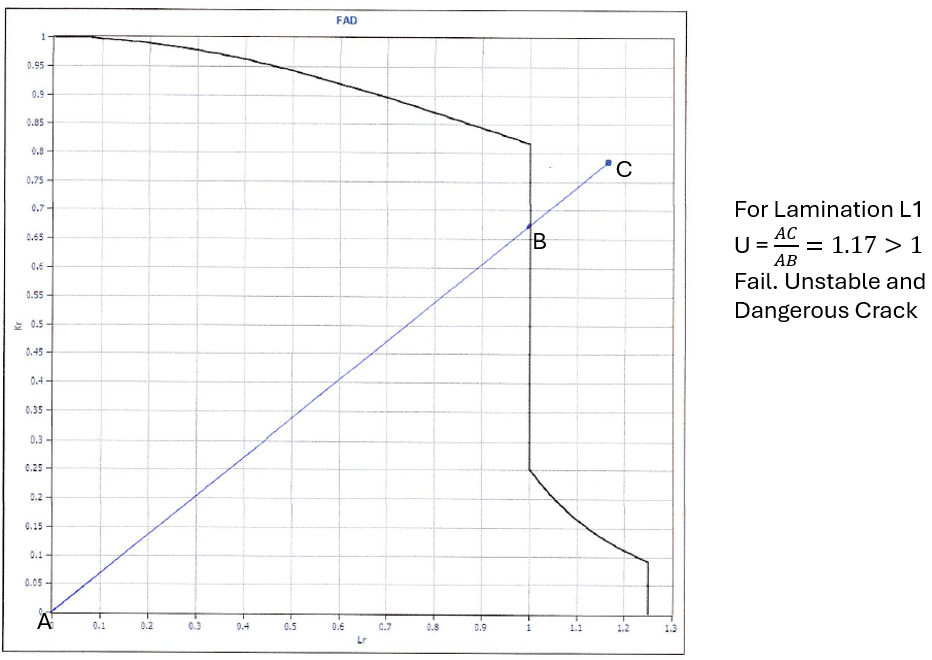
Our approach to fitness for service assessments
DOCAN can perform FFS assessments on new systems and designs to verify their integrity in the early development stages, or for operational systems which have known defects.
Our approach is pragmatic using the most suitable techniques and technology for the problem at hand. We can cover local or general corrosion, fire damage, crack-like flaws, brittle materials, mechanical damage such as dents and gouges, metallurgical defects, or even potential overload and re-rates which may require a detailed assessment.
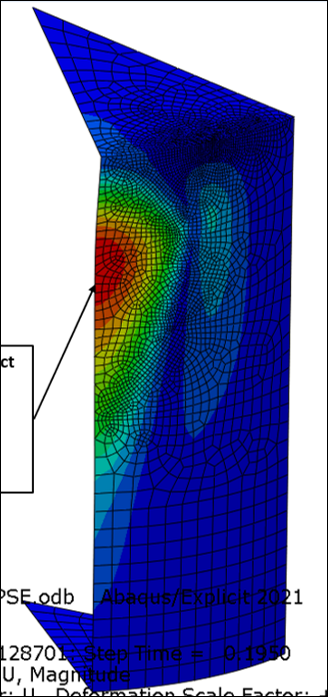
We have access to industry-leading software including ABAQUS and Ansys and our partnerships with global software houses mean we can utilise various state-of-the-art packages to perform accurate assessments.
For our clients, this means we can provide a quantitative measure of the structural integrity of any plant component or welded structure, and make appropriate run-repair-replace decisions, resulting in a cost-effective, reliable and safe solution.
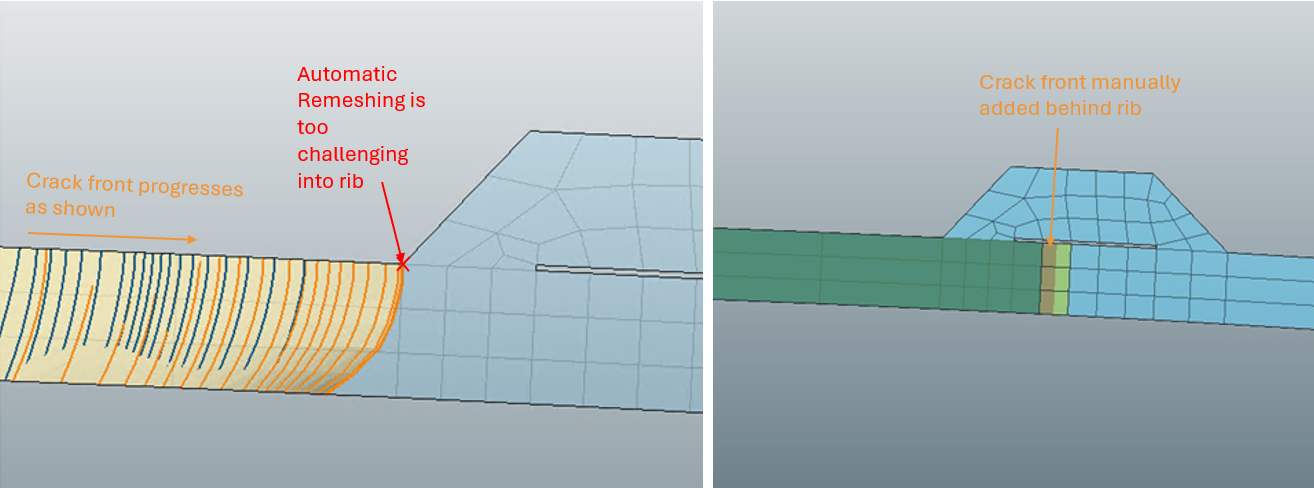
How we’ve helped our clients
Some of our recent Fitness for Service Assessments for our clients include:
- General and local metal loss using codified methods through to fully non-linear FEA.
- Use of API 579 methods covering equipment designed under ASME BPVC, British Standards, and Eurocodes.
- Crack like defects in piping systems, pressure vessels, and large welded steel structures.
- Use of BS 7910 methods using manual calculations, Crackwise assessment software using FAD approach, and Zencrack/FEA defect modelling software.
- Including defects in H2S environments and Hydrogen Induced Corrosion (HIC) damage.
- Fire damaged structures subject to thermally induced distortion and damage.
- Includes Digital Twinning to account for real geometrical effects.
- Creep damage in high temperature (+700C) applications.
- Fatigue damage.
- Laminations.
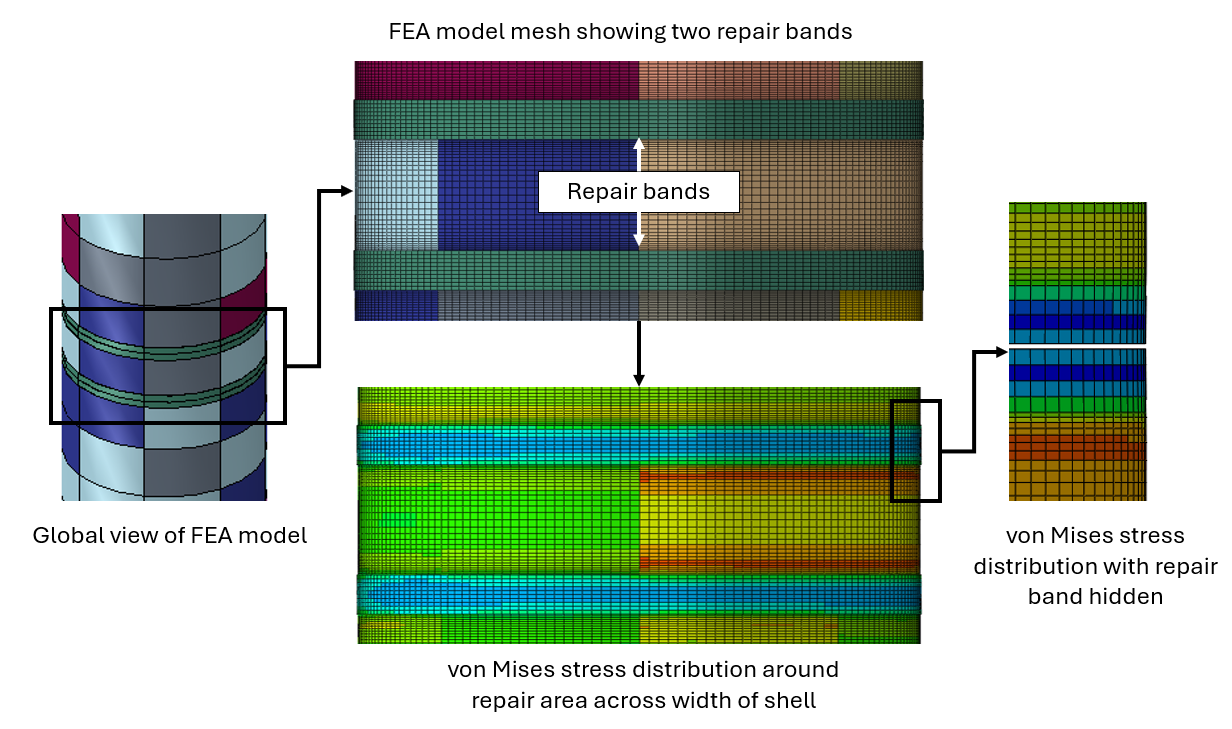
Our Tools
Info pack
To find out more about our Fitness for Service Assessment consultancy services, download our info pack.
Why choose DOCAN’s FFS assessment services?
DOCAN have a proven track record of successfully completing FFS assessments on a wide range of different components and assets, supporting our clients in ensuring that their systems meet regulatory requirements time and time again.
At our core, we’re a team of highly skilled engineers with specialist expertise in FFS and defect assessments, with the ability to identify any form of corrosion, fatigue or fracture and devise a feasible solution. Refined over many years, our structured approach is in-depth and accurate, and can be applied to an array of applications no matter the complexity or scale of the challenge.
With every project, we share the same goal: to deliver our clients a cost-effective, safe and reliable solution to their engineering challenges.
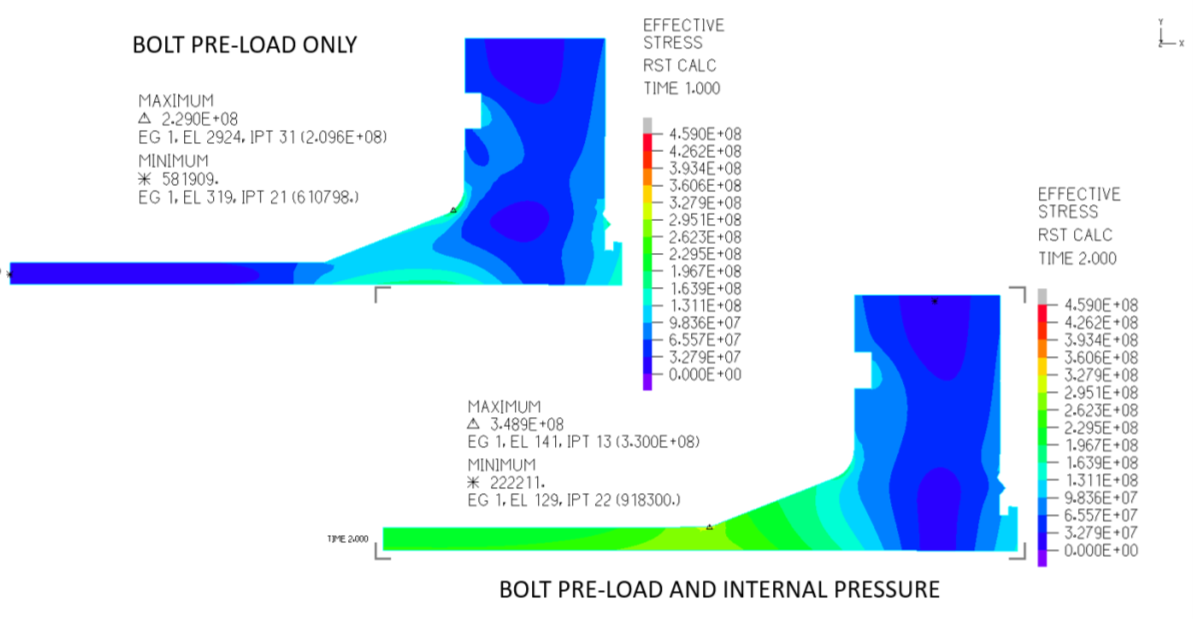