Projects
Structural assessment for pressure vessel defects
Industry
Oil & Gas
Services
Repair, FFS, Engineering Drawings, Specifications
Location
UK
One of DOCAN’s clients had discovered corrosion under insulation (CUI) around multiple insulation support rings of their pressure vessel that needed repair. DOCAN were required to perform an assessment to verify that repairs could be conducted whilst still maintaining the structural integrity of the vessel.
The challenge
Due to the shear size of the pressure vessel column, around 75m height, it was required that repairs were conducted with the column in situ, the consequence of failure would disable this expensive piece of equipment and potential cause catastrophic damage to the nearby site.
To reach these repair locations, significant towers or scaffolding were required, and these would require the support of the vessel to resist wind loads. To expedite repair operations to within the turnaround time scale multiple repairs would be conducted concurrently.
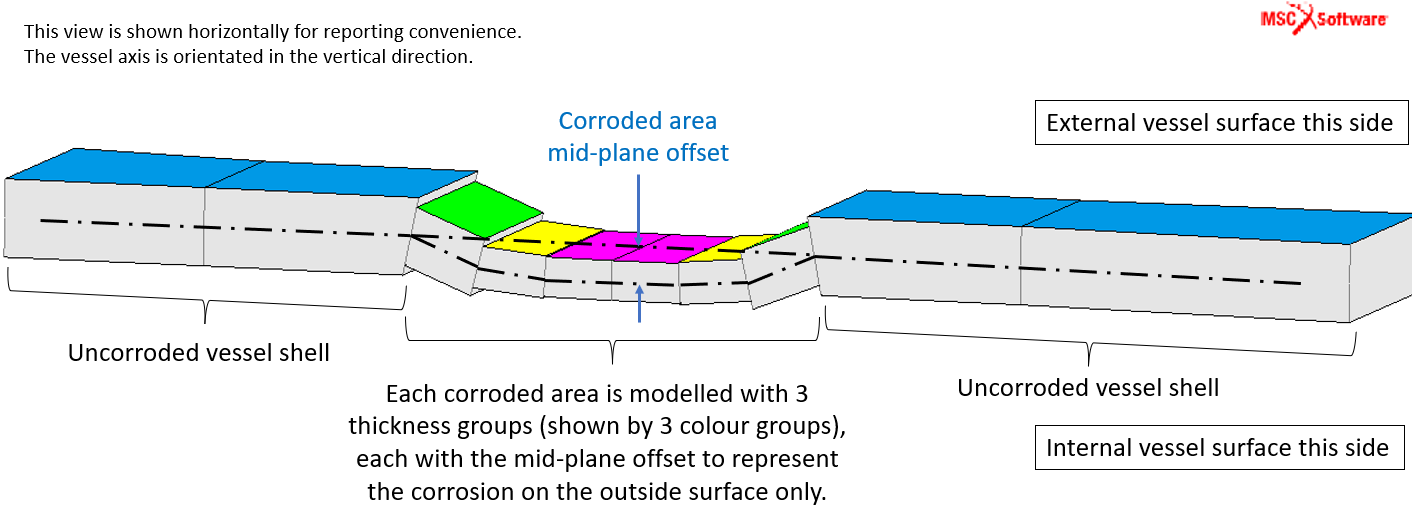
The DOCAN solution
Working to the necessary codes and standards, including BE EN 1991 (Eurocode 1), API 510, API 579, ASME VIII Div. 2, and ASME PCC-2, DOCAN performed Fitness for Service assessments of the vessel with CUI to evaluate the current structural integrity.
Several layers of analysis including linear and non-linear Finite Element Analysis (FEA) was then conducted to investigate possible repair options and the effects on the vessel during these repairs. This included evaluating the effect of wind loading on the sheeted scaffolding and the corresponding force transfer to the column while the vessel had holes cut out of its shell.
Regular correspondence was had with other sub-contractors to understand which repair strategies were feasible, providing the practical knowledge to help DOCAN optimize the proposed repair scheme. Welding simulation was used in Simufact Welding to determine the extent of the Heat Affected Zone (HAZ).
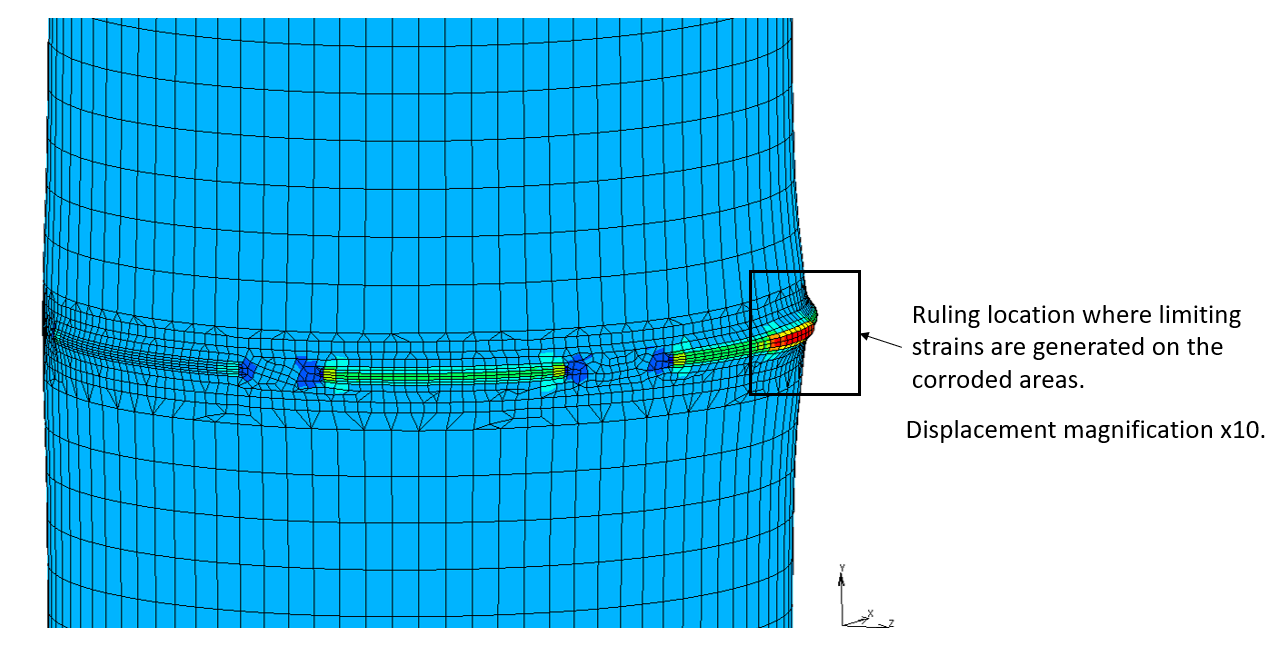
This analysis led to the design of repair cut-outs and optimal installation sequencing was investigated to speed up repairs whilst maintaining structural integrity. The effect of multiple reinforcement options was investigated as this would allow repairs to be conducted simultaneously without fearing compounding the weakening of vessel strength and structural integrity.
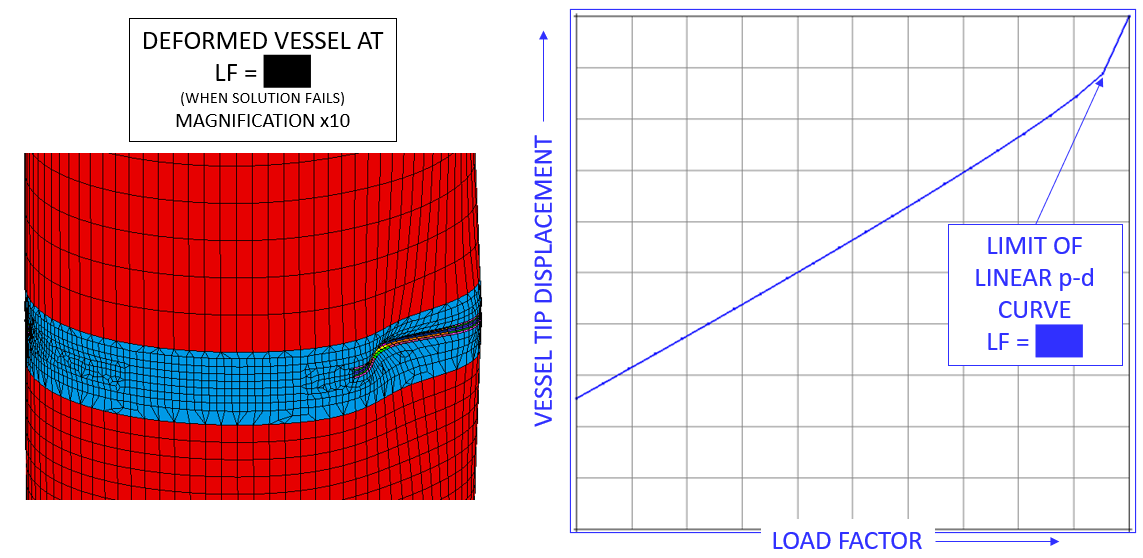
The outcome
DOCAN were able to demonstrate that the structural integrity of the column would be maintained throughout the turnaround by following the formal repair strategy which also satisfied scheduling requirements of the turnaround. Detailed design of the repairs could then be completed based on the design envelope determined by the structural assessment.
Project summary
Task | Application | DOCAN expertise | Pressure Vessels | FFSA | Repairs | Solidworks | MSC APEX | MSC MARC | PV Elite | DSET | MAPLE | Wind loading | Simufact |
---|---|---|---|---|---|---|---|---|---|---|---|---|---|
Proficiency in use of engineering standards | ASME VIII Div 1 | ![]() | ![]() | ![]() | ![]() | ![]() | ![]() | ![]() | ![]() | ![]() | ![]() | ![]() | ![]() |
ASME VIII Div 2 | ![]() | ![]() | ![]() | ![]() | ![]() | ![]() | ![]() | ![]() | ![]() | ![]() | ![]() | ![]() |
|
API 579 | ![]() | ![]() | ![]() | ![]() | ![]() | ![]() | ![]() | ![]() | ![]() | ![]() | ![]() | ![]() |
|
BS EN 1-4-1991 | ![]() | ![]() | ![]() | ![]() | ![]() | ![]() | ![]() | ![]() | ![]() | ![]() | ![]() | ![]() |
|
API 510 | ![]() | ![]() | ![]() | ![]() | ![]() | ![]() | ![]() | ![]() | ![]() | ![]() | ![]() | ![]() |
|
PCC-2 | ![]() | ![]() | ![]() | ![]() | ![]() | ![]() | ![]() | ![]() | ![]() | ![]() | ![]() | ![]() |
|
Engineering calculations | Wind pressure calculation | ![]() | ![]() | ![]() | ![]() | ![]() | ![]() | ![]() | ![]() | ![]() | ![]() | ![]() | ![]() |
True stress-strain curve calculation | ![]() | ![]() | ![]() | ![]() | ![]() | ![]() | ![]() | ![]() | ![]() | ![]() | ![]() | ![]() |
|
Thermal expansion | ![]() | ![]() | ![]() | ![]() | ![]() | ![]() | ![]() | ![]() | ![]() | ![]() | ![]() | ![]() |
|
Buckling analysis post-processing | ![]() | ![]() | ![]() | ![]() | ![]() | ![]() | ![]() | ![]() | ![]() | ![]() | ![]() | ![]() |
|
Pressure vessel modelling | Wind loading overturn moments | ![]() | ![]() | ![]() | ![]() | ![]() | ![]() | ![]() | ![]() | ![]() | ![]() | ![]() | ![]() |
MDMT | ![]() | ![]() | ![]() | ![]() | ![]() | ![]() | ![]() | ![]() | ![]() | ![]() | ![]() | ![]() |
|
Vessel design code check | ![]() | ![]() | ![]() | ![]() | ![]() | ![]() | ![]() | ![]() | ![]() | ![]() | ![]() | ![]() |
|
Minimum wall thickness | ![]() | ![]() | ![]() | ![]() | ![]() | ![]() | ![]() | ![]() | ![]() | ![]() | ![]() | ![]() |
|
CAD modelling | 3D system modelling | ![]() | ![]() | ![]() | ![]() | ![]() | ![]() | ![]() | ![]() | ![]() | ![]() | ![]() | ![]() |
Client visualisation | ![]() | ![]() | ![]() | ![]() | ![]() | ![]() | ![]() | ![]() | ![]() | ![]() | ![]() | ![]() |
|
Vessel reinforcement concepting | ![]() | ![]() | ![]() | ![]() | ![]() | ![]() | ![]() | ![]() | ![]() | ![]() | ![]() | ![]() |
|
Virtual Reality walk through | ![]() | ![]() | ![]() | ![]() | ![]() | ![]() | ![]() | ![]() | ![]() | ![]() | ![]() | ![]() |
|
FEA modelling | Reviewing stl surface scan data | ![]() | ![]() | ![]() | ![]() | ![]() | ![]() | ![]() | ![]() | ![]() | ![]() | ![]() | ![]() |
Meshing - Rebuilding and refining without geometry | ![]() | ![]() | ![]() | ![]() | ![]() | ![]() | ![]() | ![]() | ![]() | ![]() | ![]() | ![]() |
|
Fitness For Service Assessment | Level 3 assessment | ![]() | ![]() | ![]() | ![]() | ![]() | ![]() | ![]() | ![]() | ![]() | ![]() | ![]() | ![]() |
Linear elastic analysis | ![]() | ![]() | ![]() | ![]() | ![]() | ![]() | ![]() | ![]() | ![]() | ![]() | ![]() | ![]() |
|
Non-linear elastic-plastic collapse | ![]() | ![]() | ![]() | ![]() | ![]() | ![]() | ![]() | ![]() | ![]() | ![]() | ![]() | ![]() |
|
Buckling analysis | ![]() | ![]() | ![]() | ![]() | ![]() | ![]() | ![]() | ![]() | ![]() | ![]() | ![]() | ![]() |
|
Drawings | BS8888 | ![]() | ![]() | ![]() | ![]() | ![]() | ![]() | ![]() | ![]() | ![]() | ![]() | ![]() | ![]() |
Repair design | ![]() | ![]() | ![]() | ![]() | ![]() | ![]() | ![]() | ![]() | ![]() | ![]() | ![]() | ![]() |
|
GD&T | ![]() | ![]() | ![]() | ![]() | ![]() | ![]() | ![]() | ![]() | ![]() | ![]() | ![]() | ![]() |
|
Welding review | Welding simulation & sensitivity studies | ![]() | ![]() | ![]() | ![]() | ![]() | ![]() | ![]() | ![]() | ![]() | ![]() | ![]() | ![]() |
Technical drawings | Pressure vessel repair drawings | ![]() | ![]() | ![]() | ![]() | ![]() | ![]() | ![]() | ![]() | ![]() | ![]() | ![]() | ![]() |