Our core tools
Rotating Equipment Design
As a Registered Partner with SoftInWay, DOCAN integrates the robust capabilities of AxSTREAM for Turbomachinery Design into our consultancy services, enabling us to deliver cutting-edge solutions for complex rotating equipment and turbomachinery challenges.
Why we use AxSTREAM for turbomachinery design
At DOCAN, we pride ourselves on offering our clients industry-leading solutions and we utilise AxSTREAM for turbomachinery design software because it’s the gold standard for rotating equipment design.
Its robust capabilities allow us to address complex engineering across a wide range of industries, including energy, aerospace, and manufacturing. By integrating AxSTREAM into our consulting services, we ensure our designs are not only innovative but also precise, efficient, and tailored to the specific needs of our clients.
AxSTREAM’s unique combination of 1D-3D design tools, advanced simulation capabilities, and generative design functionality enables us to streamline the entire design process, from initial concepts to performance optimisation. This ensures that our clients benefit from reduced development time, lower costs, and designs that are fully optimised for real-world performance.
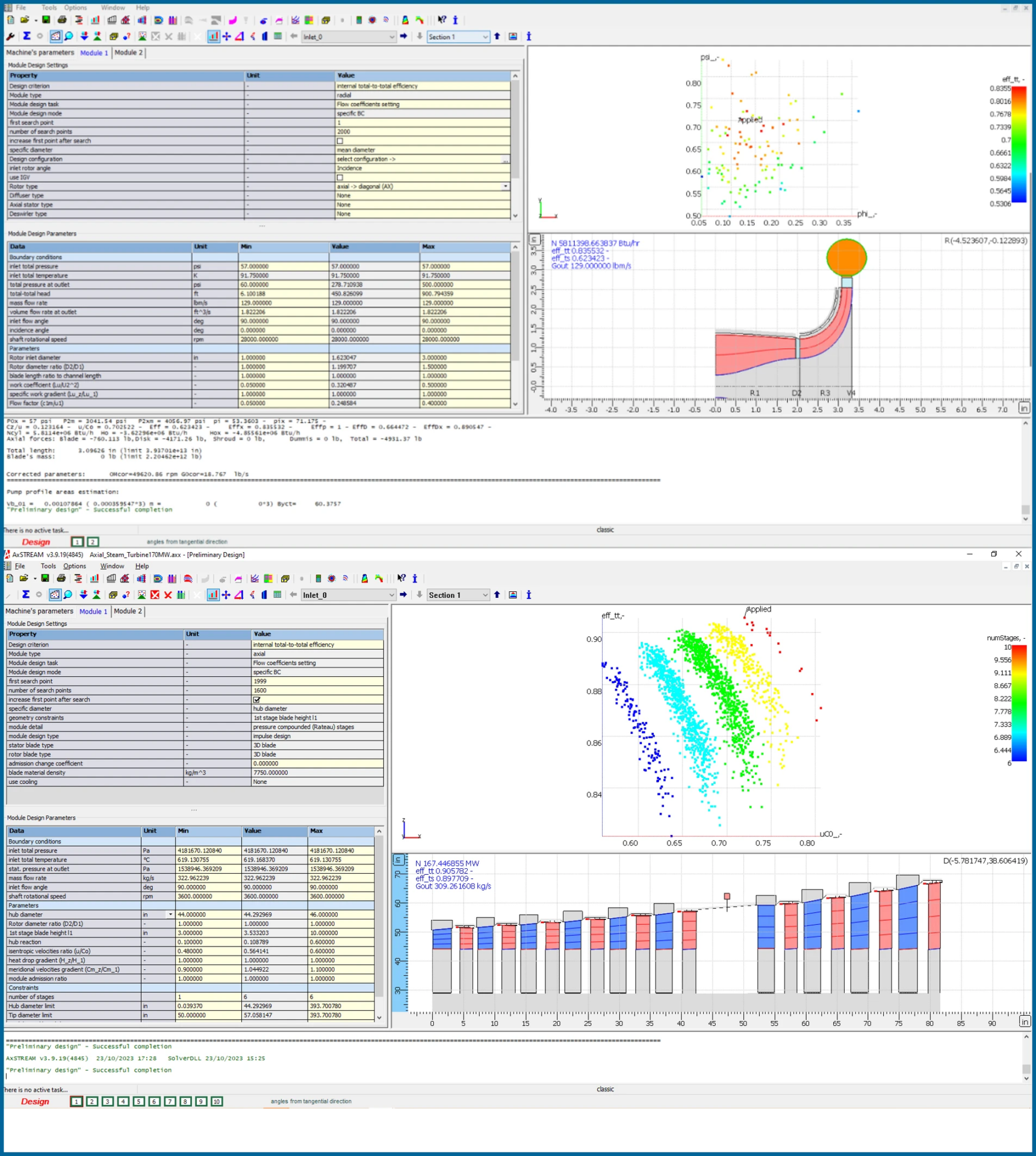
Core capabilities and benefits
AxSTREAM provides a comprehensive suite of tools that optimise rotating equipment design across every stage of the process. Its range of advanced features include:
- Generative preliminary design: Quickly generate thousands of design geometries, allowing us to explore multiple configurations (e.g., axial vs. radial, number of stages) and narrow down to the most effective solutions. It enables early architecture decisions, saving resources and time while optimising geometry.
- 1D-3D turbomachinery design & analysis: Predict performance, choke (compressors), and cavitation (pumps) early in the design phase. With fast 1D/2D solvers and the ability to perform parametric studies and create 3D flow paths, AxSTREAM allows for quick iteration and detailed performance analysis, while also enabling reverse engineering of existing machines.
- Advanced 3D CFD & FEA: Integrated CFD and FEA capabilities streamline the process of optimising turbomachinery under real-world conditions. AxSTREAM’s parallel processing and flexible export options for geometry or mesh make it efficient for quick design iterations.
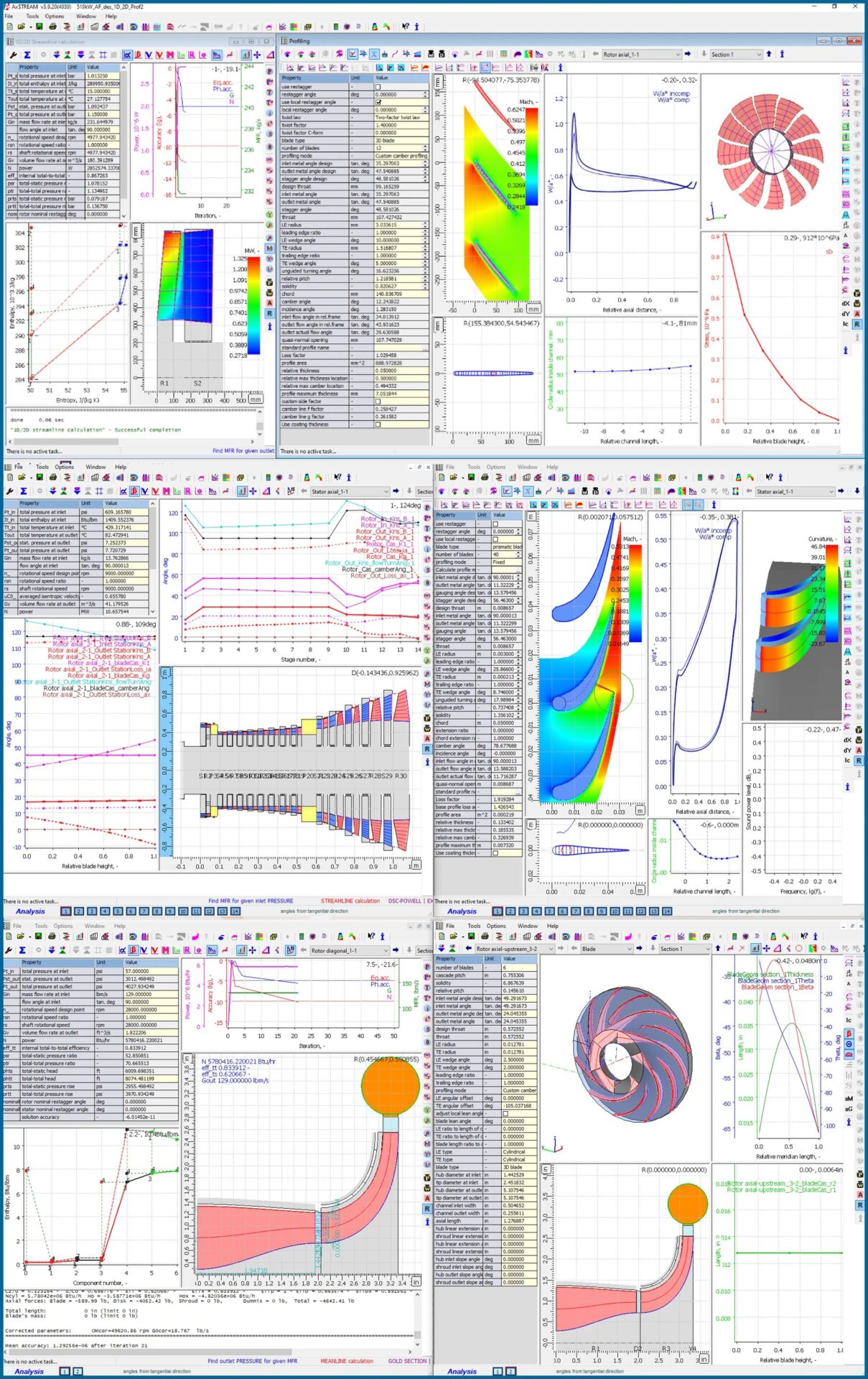
AxSTREAM Rotor Dynamics
AxSTREAM Royor Dynamics is a state-of-the-art software tool that offers advanced simulation and analysis to predict and prevent performance issues such as instability in rotors and bearings.
This tool enables us to ensure machines operate reliably and efficiently under various conditions, with its capabilities including:
- Comprehensive rotor analysis: Predict critical speeds, stability, and response to unbalanced or harmonic forces. AxSTREAM helps identify potential issues early, preventing resonance and instability in the design phase.
- Advanced bearing modelling: Model various bearing types—including sliding, rolling, and magnetic bearings—to optimise rotor performance under different conditions.
- Dynamic response prediction: Analyse rotor behaviour under operational stresses, ensuring designs are stable and reliable. The tool also supports both linear and nonlinear analysis for a wide range of rotor behaviours.
- Efficient integration with turbomachinery design: Rotor dynamics analysis can be seamlessly integrated with the broader turbomachinery design process, eliminating the need for separate CAD workflows and ensuring timely, accurate results.
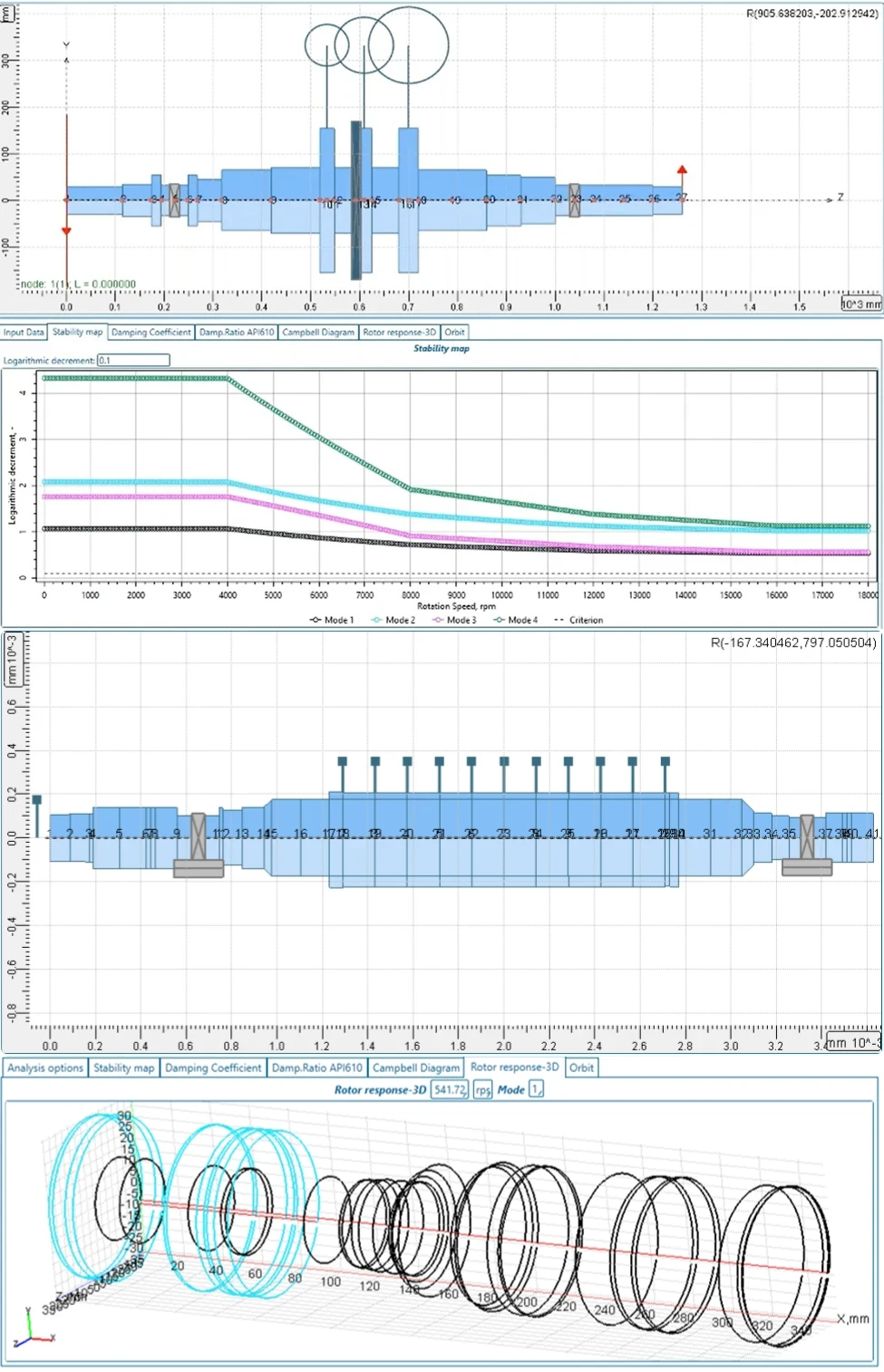
How our rotating equipment design services can help you
One of our specialities here at DOCAN is delivering advanced rotating equipment and turbomachinery solutions using AxSTREAM’s world-class turbomachinery design software. From concept to completion, we combine deep expertise with cutting-edge technology to develop innovative, reliable systems that are tailored to your specific requirements.
Whether you need to optimise existing equipment, design entirely new systems, or solve complex engineering challenges, DOCAN can help.
Our partnership with SoftInWay means that not only do we use AxSTREAM’s powerful capabilities in our consultancy projects, but we can also provide our clients with direct access to this industry-leading software.
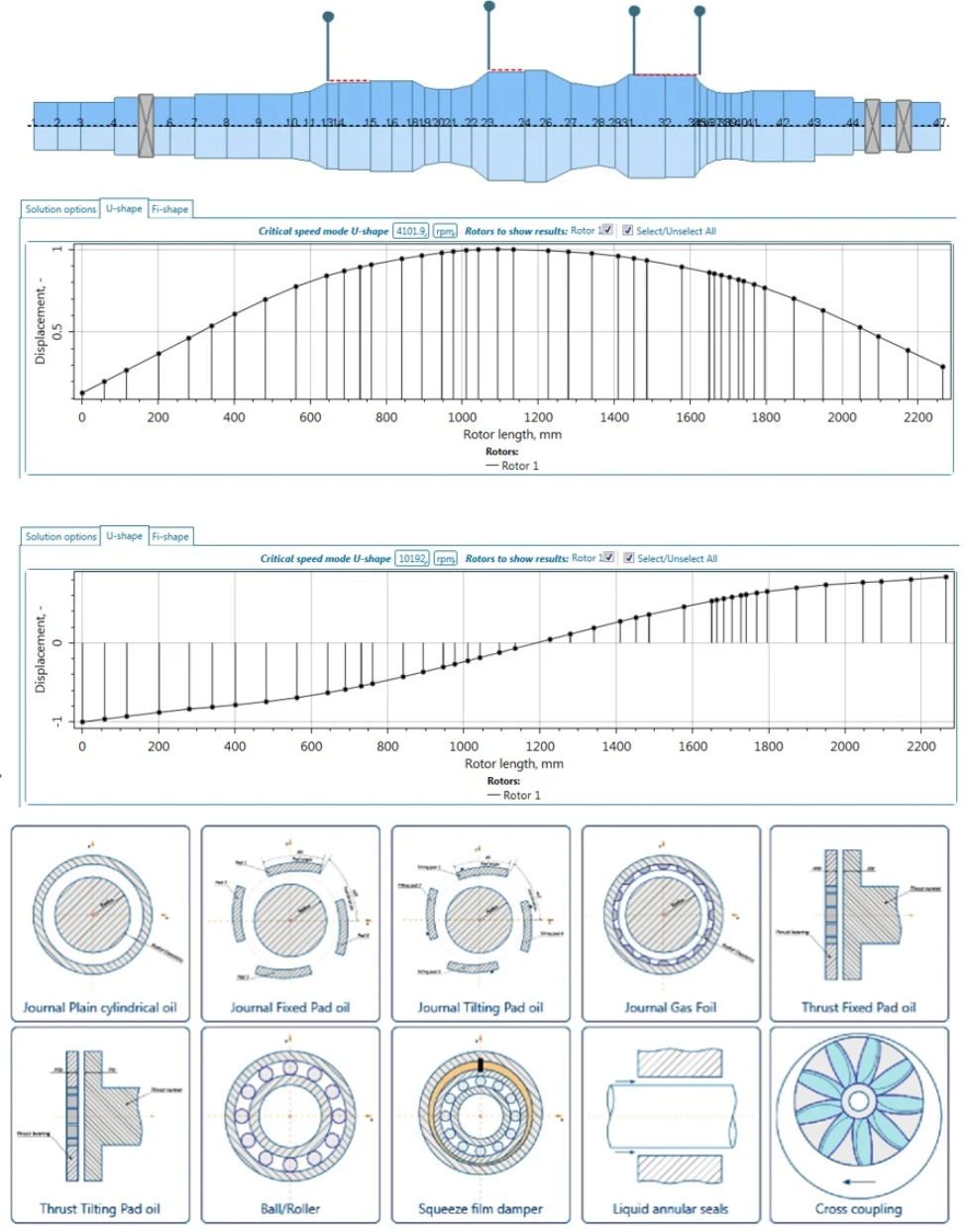
Working with DOCAN
Working with DOCAN, you have direct access to a large network of experienced professionals and industry-leading software to drive your project forward. If you want to know how we can help, get in touch with us.