Projects
Analysis and Design Services for development Rotating Control Device (RCD) components
Industry
Oil & Gas
Services
FEA, Design by analysis
Location
USA - Texas (Houston)
DOCAN have provided engineering analysis and design support services to a client in the drilling industry.
The work was based on a part of a Rotating Control Device (RCD) used to control flow and pressure within a drill string subjected to high pressures.
The challenge
DOCAN have worked to develop the design of the RCD component from an initial design into a design code compliant system. In addition to having extensive industry experience within the Mining Industry, we also use state-of-the art design and analysis tools to complete our work MSC Apex and MARC, available through the MSCOne plan. For this project we worked to design code API 16RCD, API 6X and API 6A to deliver a suitable design.
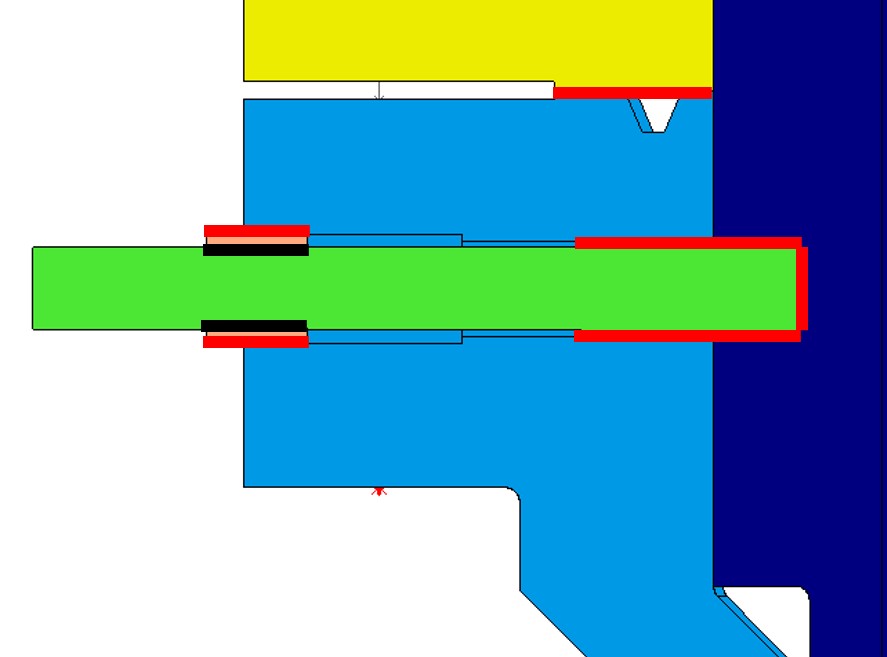
The DOCAN solution
Starting simply, we employed Maple, a mathematical calculation software to perform upfront calculations. Maple allowed us to easily build complex calculations which can be checked and audited. In this case, we calculated minimum design code wall thickness requirements and determined load transfer between parts to perform initial sizing of components.
We actively communicate with our clients to work to an optimal solution which satisfies their requirements to ensure the best chances of a design working prior to our detailed assessment work, reducing the need for reassessment and hassle for the client.
Next, we created and modified 3D CAD geometry using MSC Apex software. Apex was used to export standard geometry files giving the ability to transfer CAD to Solidworks, allowing the client the option to produce detailed technical drawings with no further 3D CAD file editing.
Assessment and analysis was then performed using the MSC MARC Finite Element Analysis (FEA) software. For this project, we analysed the complex interaction of multiple components, including frictional contact, allowances for clearances between parts, and bolting pre-loads. We also employed fully non-linear material models to account for material plasticity. A DOCAN Maple calculation tool has been developed allowing these properties to be set up and imported FEA with minimal user effort.
The Outcome
The results from the FEA analysis showed that with our suggested modifications, the stresses were design code-compliant, and thus acceptable for the client.
In addition to commercially available simulation software, we use custom DOCAN calculation tools to perform code checks such as the stress linearization required for our assessment. This is an example of the DSET (DOCAN Stress Engineering Tools), in addition to creating these tools for our own use, DOCAN can develop custom tools for our clients to use to automate and streamline their engineering calculation tasks.
DOCAN reports offer clear and concise feedback to the client showing the results of our work and also the design information required to achieve a suitable design. In this case, the client had confidence that the design was suitable for use and could proceed to manufacture and delivery of the assembly to their customers in the field.
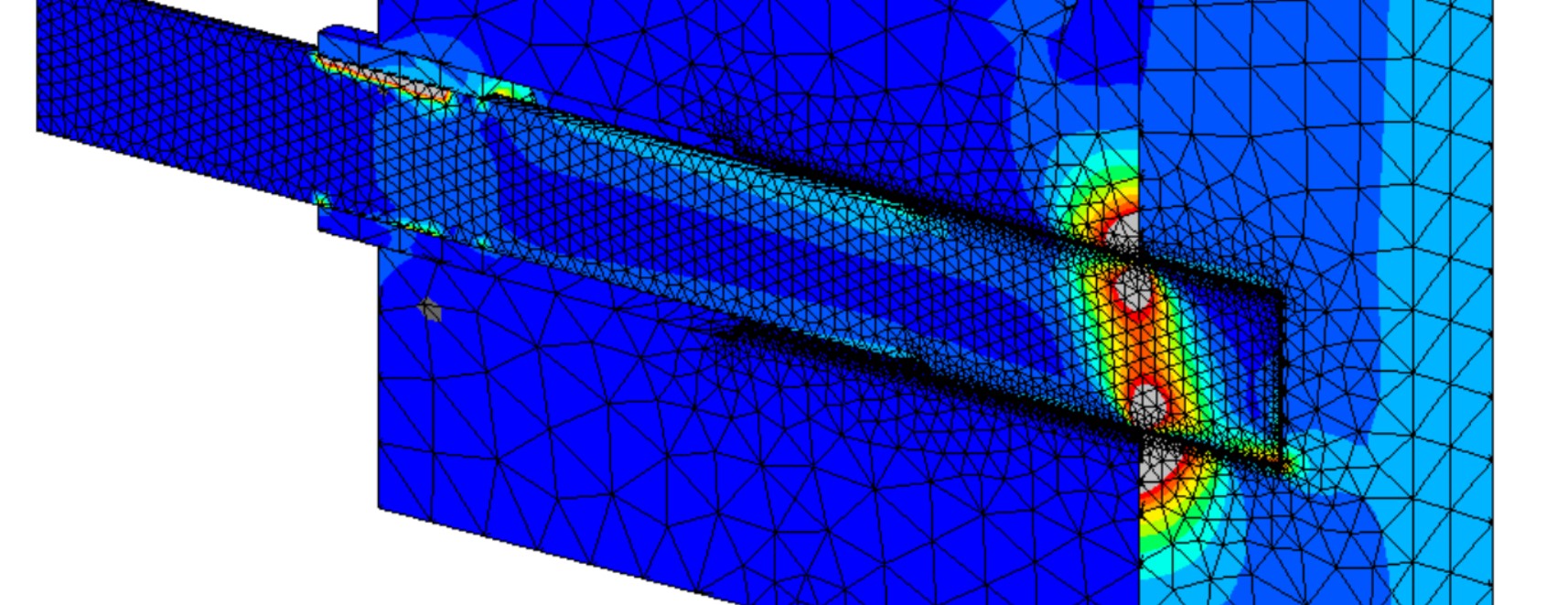
Project Summary
Task | Application | DOCAN design expertise | Rotating Control Device (RCD) Assessment | Solidworks | MSC APEX | MSC MARC | DSET | Maple |
---|---|---|---|---|---|---|---|---|
Proficiency in use of engineering standards | ASME VIII Div 2 | ![]() | ![]() | ![]() | ![]() | ![]() | ![]() | ![]() |
API 6X & 6A | ![]() | ![]() | ![]() | ![]() | ![]() | ![]() | ![]() |
|
API 16RCD | ![]() | ![]() | ![]() | ![]() | ![]() | ![]() | ![]() |
|
CAD Geometry | Defeaturing client geometry | ![]() | ![]() | ![]() | ![]() | ![]() | ![]() | ![]() |
Performing design iterations | ![]() | ![]() | ![]() | ![]() | ![]() | ![]() | ![]() |
|
Tolerance stack-up | ![]() | ![]() | ![]() | ![]() | ![]() | ![]() | ![]() |
|
FEA model building | Meshing | ![]() | ![]() | ![]() | ![]() | ![]() | ![]() | ![]() |
Forces & boundary conditions | ![]() | ![]() | ![]() | ![]() | ![]() | ![]() | ![]() |
|
Design Code Assessment | Linear elastic analysis | ![]() | ![]() | ![]() | ![]() | ![]() | ![]() | ![]() |
Non-linear elastic-plastic collapse | ![]() | ![]() | ![]() | ![]() | ![]() | ![]() | ![]() |
|
Non-linear contact & clearances | ![]() | ![]() | ![]() | ![]() | ![]() | ![]() | ![]() |
|
Sensitivity studies | ![]() | ![]() | ![]() | ![]() | ![]() | ![]() | ![]() |
|
Engineering Calculations | Stress Linearization (DSET) | ![]() | ![]() | ![]() | ![]() | ![]() | ![]() | ![]() |
Stress & tmin calcs | ![]() | ![]() | ![]() | ![]() | ![]() | ![]() | ![]() |
|
True stress-strain curve calculation | ![]() | ![]() | ![]() | ![]() | ![]() | ![]() | ![]() |