Projects
Crack-like defect Fitness-For-Service assessment
DOCAN have experience performing many Fitness-For-Service (FFS) assessments, including FFS of crack-like defects in critical components, such as piping and pressure vessels.
To improve the accuracy and efficiency of our assessments and ensure safety, Crackwise Software is utilised to assist in the assessments.
Crackwise is a leading Fitness for Service software, designed to accurately evaluate the integrity of pipelines, pressure equipment and structures that contain flaws. For more information, see the Crackwise software page.
The challenge
Recently, DOCAN have been employed to assess a series of piping systems that contain a significant number of crack-like defects requiring a FFS assessment to code BS7910. As our team is highly proficient in using Crackwise to its full potential, this allowed DOCAN to utilise its tools to complete the assessment of all crack defects accurately and efficiently.
The identified pipelines for assessment were highly critical lines that had suffered H2S damage and were all of different specifications and design conditions with defects at different locations. Consequently, numerous defect assessments were required to cover all identified defect scenarios.
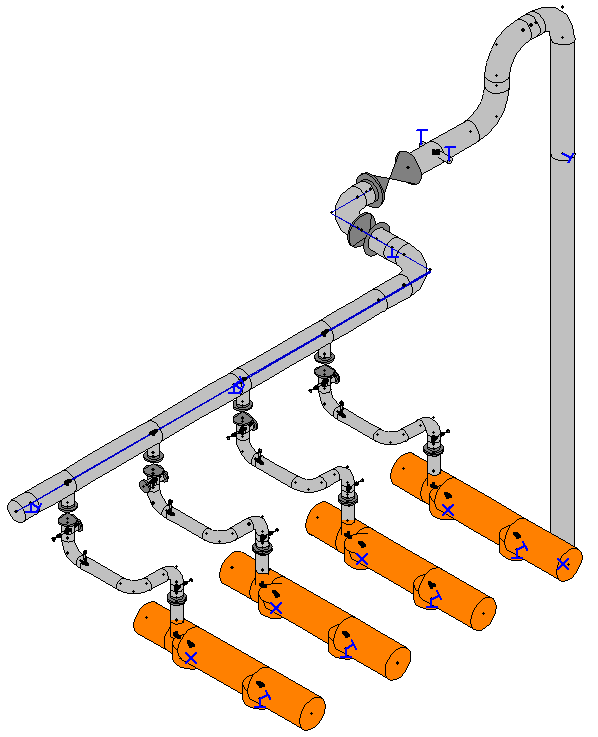
The DOCAN Solution
There were many inputs and variables required to complete the BS7910 assessment, these needed to be determined and justified for input into Crackwise. These included:
- Fracture toughness: Fracture toughness for each defect different and, it was calculated for each defect using API579 code rules.
- Relaxation of residual stresses: Has the weld been post weld heat treated to reduce the residual stresses?
- Appropriate temperature dependent material properties for each defect location.
The stress acting at every defect location was unknown due to different design conditions and locations, therefore the maximum design code allowable stress and the stress due to internal design pressure were used as a basis of the assessment. Where, more detail was required to achieve a more accurate result, pipe stress analysis models were produced to achieve accurate stresses for use in the defect assessments.
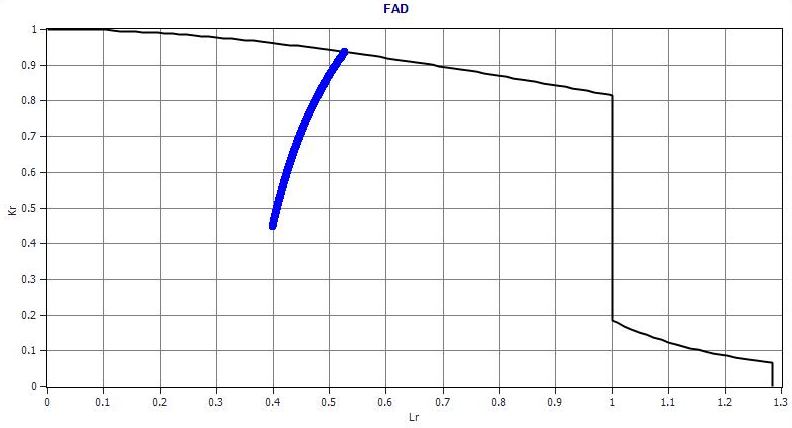
The outcome
The results of the assessments identified which of the defects needed to be addressed immediately, which are acceptable in the immediate future but would need close monitoring and which are fit for continued operation.
The client had further lines that would require FFS of cracklike defects. DOCAN developed an engineering tool to increase the efficiency of assessing defects in the future. The tool allows the client to enter a pipe size, specification number and defect size and with output the result of the FFS assessment. This tool forms part of our suite of engineering tools that are available called DSET (DOCAN Stress Engineering Tools).
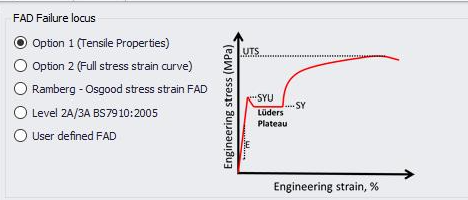
Some key features of Crackwise that were utilised include:
- Critical depth analysis – determines the critical depth at which the flaw becomes unacceptable, preventing numerous iterations being required to identify the critical depth size.
- Batch runner – allows thousands of defects to be assessed simultaneously in one batch analysis with all specified combinations of variables, speeding up pre and post processing for the assessment.
- Automatic coefficient calculations – numerous steps of the assessment process following BS7910 require coefficients to be looked up and calculated in the code, Crackwise is able to automatically find and execute these calculations when supplied with the correct input data
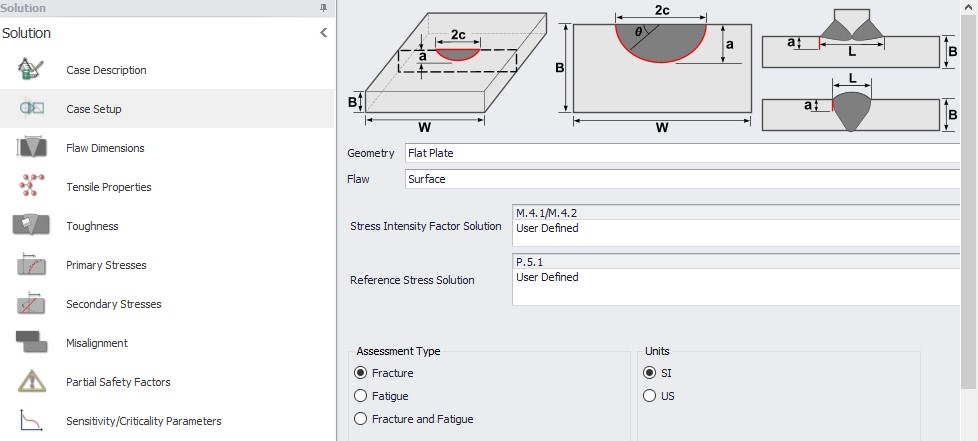
If your project demands highly complex FFS assessments, crack-like defect analyses or strategic structural repairs, we can help. Working with DOCAN, you have direct access to a large network of experienced professionals and industry-leading software to drive your project forward. If you want to know how we can help, get in touch with us.