Projects
Design by assessment for
thrust testing assemblies
Industry
Defence
Services
FEA, Design by analysis
Location
UK
DOCAN have worked to provide design and analysis services to a client who produces pressure systems equipment.
The client required a jet thrust testing system to be designed which would be retrofit into a standard size ISO container, which would form part of the load bearing structure.
The challenge
The large forces produced by the jet thrust system required a strong frame design to protect the sensitive system components, whilst giving the client flexibility to change the configuration of the test equipment to accommodate different test parameters.
Part of DOCAN’s scope of work was to provide marked-up engineering drawings for manufacture and to verify the capacity of the containers lifting points for transportation purposes, with the much heavier test system installed.
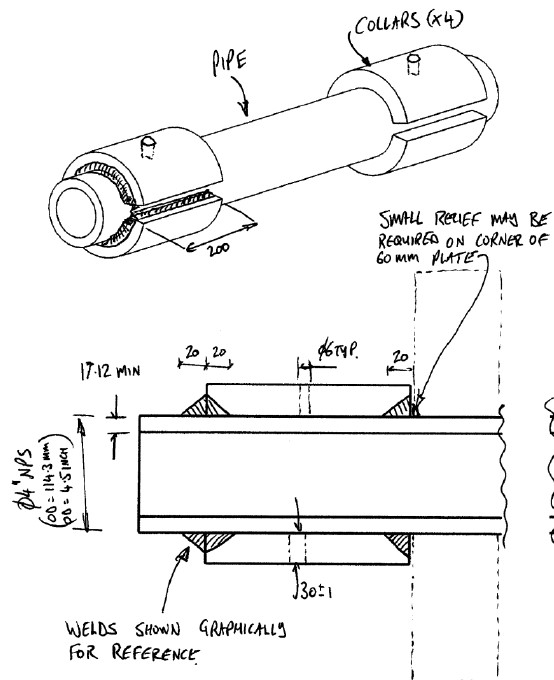
The DOCAN solution
We approached this project from first principles, using a combination of manual calculations and beam element FEA modelling in MSC MARC to size the main structural members, following EC3 design rules. This allows for several design iterations to be quickly explored. More detailed shell and solid element FEA modelling was then used to assess the detailed locations of the design. As part of the project, DOCAN’s engineers developed an innovative bolting arrangement which could be used to quickly change the configuration of the equipment to suit the client’s needs.
Due to the different aspects of the testing system, we performed the assessment using Eurocode, DNV and ASME Piping design codes to show the components were suitable to carry the massive thrust loads which would be applied during use.
The Outcome
DOCAN delivered a design of a safe, cost effective system which met the client’s requirements. We also delivered a detailed drawing pack, giving the client advice on manufacture of components and construction of the welded and bolted assembly.
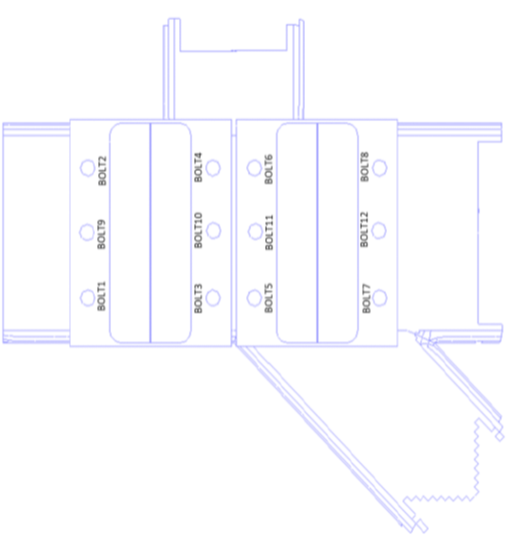
Project Summary
Item | Application | DOCAN design expertise | Assessment of fabricated structures | Solidworks | FEA | Pipe Stress | MAPLE |
---|---|---|---|---|---|---|---|
Proficiency in use of engineering standards | ASME B31.3 | ![]() | ![]() | ![]() | ![]() | ![]() | ![]() |
ASME II PART D | ![]() | ![]() | ![]() | ![]() | ![]() | ![]() |
|
ASME VIII Div. 2 | ![]() | ![]() | ![]() | ![]() | ![]() | ![]() |
|
EC3 Eurocode | ![]() | ![]() | ![]() | ![]() | ![]() | ![]() |
|
DNV 2.7-1 | ![]() | ![]() | ![]() | ![]() | ![]() | ![]() |
|
Equipment design | Test rig | ![]() | ![]() | ![]() | ![]() | ![]() | ![]() |
Jet thrust loading | ![]() | ![]() | ![]() | ![]() | ![]() | ![]() |
|
DNV ISO container | ![]() | ![]() | ![]() | ![]() | ![]() | ![]() |
|
Fabricated structures | ![]() | ![]() | ![]() | ![]() | ![]() | ![]() |
|
Pressure systems | ![]() | ![]() | ![]() | ![]() | ![]() | ![]() |
|
Piping | ![]() | ![]() | ![]() | ![]() | ![]() | ![]() |
|
CAD geometry | 3D solid and 2D surface geometry | ![]() | ![]() | ![]() | ![]() | ![]() | ![]() |
Line modelling | ![]() | ![]() | ![]() | ![]() | ![]() | ![]() |
|
FEA | Solid / Shell / Beam modelling | ![]() | ![]() | ![]() | ![]() | ![]() | ![]() |
Parametric scripting | ![]() | ![]() | ![]() | ![]() | ![]() | ![]() |
|
Bolted connection assessment | ![]() | ![]() | ![]() | ![]() | ![]() | ![]() |
|
Pipe Stress | ![]() | ![]() | ![]() | ![]() | ![]() | ![]() |
|
Engineering calculations | Stress Linearization (DSET) | ![]() | ![]() | ![]() | ![]() | ![]() | ![]() |
Stress & tmin calcs | ![]() | ![]() | ![]() | ![]() | ![]() | ![]() |
|
True stress-strain curve calculation | ![]() | ![]() | ![]() | ![]() | ![]() | ![]() |