Projects
Fitness For Service Assessment (FFSA) of a corroded Pressure Vessel
Industry
Oil & Gas
Services
FEA, Fitness for Service, Life Extension
Location
UK
One of DOCAN’s clients had discovered internal corrosion near to a pipe support in one of their pressure vessels on their UK-based oil terminal.
DOCAN were contracted to perform a Fitness for Service Assessment to advise the client if their equipment was safe for continued service and to understand when repairs should be implemented. Due to the proximity of the corrosion to a pipe support attached to the vessel and the vessel nozzle, API579 Level 1 and Level 2 assessment methods could not be used. More complex Level 3 methods were required.
The challenge
Unfortunately, key design documents pertaining to the vessel and connected piping had been lost over years of operation. However, with DOCAN’s tools such as PV Elite, ROHR2 and MSC MARC, and our experience with them, it was possible to fill in the gaps using a range of analysis and calculation methods to facilitate the Level 3 FFSA.
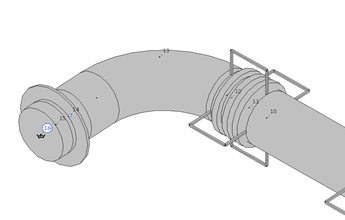
The DOCAN solution
Our main focus was to:
- Review the attached pipework and using the ROHR2 Pipe Stress Analysis software, determine nozzle and pipe support loads applied to the vessel.
- Verify the construction of the vessel within the PVElite pressure vessel assessment software to confirm missing technical information.
- Use MSC APEX software to build a comprehensive FEA model of the vessel, including modelling of the corroded areas close to the pipe support.
- Perform the L3 FFSA using MSC MARC software.
In order to gather the information required to estimate the stresses over the corroded areas, our team performed numerous sensitivity studies with the information that was available.
ROHR2 was used to conduct pipe stress analysis to accurately estimate the loads transferred on to the vessel shell due to sustained and thermal expansion effects of the pipework.
Then, PV Elite was used to model the vessel and its major attachments, to provide information such as the minimum design code thickness and shell stresses under various load cases, such as deadweight, internal pressure and wind loads calculated from BS6399.
Sensitivity studies were then performed in MSC APEX to quickly assess which key features should be considered in the full FEA assessment model. The assessment itself was performed in MSC MARC, which allowed for both linear and non-linear methods to be employed to calculate the stresses on and around the defect areas. We also investigated the levels of future corrosion which may be permissible before remedial action was required.
The Outcome
DOCAN reports offer clear and concise feedback to the client showing the results of our work. In this case, we were able to give the client confidence that the equipment was still FFS and advise when repairs should be implemented while highlighting areas for further inspection to understand when repairs were required.
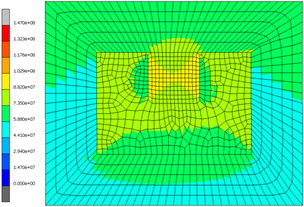
Project Summary
Task | Application | DOCAN fitness for service expertise | Pressure vessels | Pipe support & piping | Wind loading | Solidworks | MSC Apex | MSC Marc | PV Elite | ROHR2 | DSET | Maple |
---|---|---|---|---|---|---|---|---|---|---|---|---|
Proficiency in use of engineering standards | BS1515 | ![]() | ![]() | ![]() | ![]() | ![]() | ![]() | ![]() | ![]() | ![]() | ![]() | ![]() |
PD5500 | ![]() | ![]() | ![]() | ![]() | ![]() | ![]() | ![]() | ![]() | ![]() | ![]() | ![]() |
|
API 579 | ![]() | ![]() | ![]() | ![]() | ![]() | ![]() | ![]() | ![]() | ![]() | ![]() | ![]() |
|
CP3 | ![]() | ![]() | ![]() | ![]() | ![]() | ![]() | ![]() | ![]() | ![]() | ![]() | ![]() |
|
BS6399 | ![]() | ![]() | ![]() | ![]() | ![]() | ![]() | ![]() | ![]() | ![]() | ![]() | ![]() |
|
ASME B31.3 | ![]() | ![]() | ![]() | ![]() | ![]() | ![]() | ![]() | ![]() | ![]() | ![]() | ![]() |
|
Fitness For Service Assessment | Level 3 assessment | ![]() | ![]() | ![]() | ![]() | ![]() | ![]() | ![]() | ![]() | ![]() | ![]() | ![]() |
Pressure vessel modelling | Wind loading bending stress | ![]() | ![]() | ![]() | ![]() | ![]() | ![]() | ![]() | ![]() | ![]() | ![]() | ![]() |
Design checks | ![]() | ![]() | ![]() | ![]() | ![]() | ![]() | ![]() | ![]() | ![]() | ![]() | ![]() |
|
Minimum wall thickness calc | ![]() | ![]() | ![]() | ![]() | ![]() | ![]() | ![]() | ![]() | ![]() | ![]() | ![]() |
|
Pipe stress | Thermal & dead weight loading | ![]() | ![]() | ![]() | ![]() | ![]() | ![]() | ![]() | ![]() | ![]() | ![]() | ![]() |
Gimbal expansion joints | ![]() | ![]() | ![]() | ![]() | ![]() | ![]() | ![]() | ![]() | ![]() | ![]() | ![]() |
|
Pipe support design | ![]() | ![]() | ![]() | ![]() | ![]() | ![]() | ![]() | ![]() | ![]() | ![]() | ![]() |
|
Calculating nozzle loads | ![]() | ![]() | ![]() | ![]() | ![]() | ![]() | ![]() | ![]() | ![]() | ![]() | ![]() |
|
CAD Modelling | Creating 3D CAD from drawings | ![]() | ![]() | ![]() | ![]() | ![]() | ![]() | ![]() | ![]() | ![]() | ![]() | ![]() |
FEA model building | Meshing | ![]() | ![]() | ![]() | ![]() | ![]() | ![]() | ![]() | ![]() | ![]() | ![]() | ![]() |
Corrosion modelling | ![]() | ![]() | ![]() | ![]() | ![]() | ![]() | ![]() | ![]() | ![]() | ![]() | ![]() |
|
FFSA Code Assessment | Linear elastic analysis | ![]() | ![]() | ![]() | ![]() | ![]() | ![]() | ![]() | ![]() | ![]() | ![]() | ![]() |
Non-linear elastic-plastic collapse | ![]() | ![]() | ![]() | ![]() | ![]() | ![]() | ![]() | ![]() | ![]() | ![]() | ![]() |
|
Future corrosion | ![]() | ![]() | ![]() | ![]() | ![]() | ![]() | ![]() | ![]() | ![]() | ![]() | ![]() |
|
Engineering calculations | Stress & tmin calcs | ![]() | ![]() | ![]() | ![]() | ![]() | ![]() | ![]() | ![]() | ![]() | ![]() | ![]() |
True stress-strain curve calculation | ![]() | ![]() | ![]() | ![]() | ![]() | ![]() | ![]() | ![]() | ![]() | ![]() | ![]() |