Projects
Wind loading for Fitness for Service Assessment
Industry
Oil & Gas
Services
Repair, FFS, Engineering Drawings, Specifications
Location
UK
One of DOCAN’s clients had discovered external corrosion around the insulation support rings of their pressure vessel that needed repair. DOCAN were required to perform a FFS assessment of the vessel in its current state, during repairs, and in the repaired state.
The challenge
Thanks to previous work performed by DOCAN, an effective repair plan had been arranged involving removing and replacing large sections of damaged vessel wall. This means during repair there would be sections of decreased strength while material was missing.
It was considered that a strong unexpected gust may consequently endanger the success of the repair operation. Detailed wind loading assessment was required to consider the attachments to the vessel required for the repairs and the various ways the vessel would be weakened mid repair.
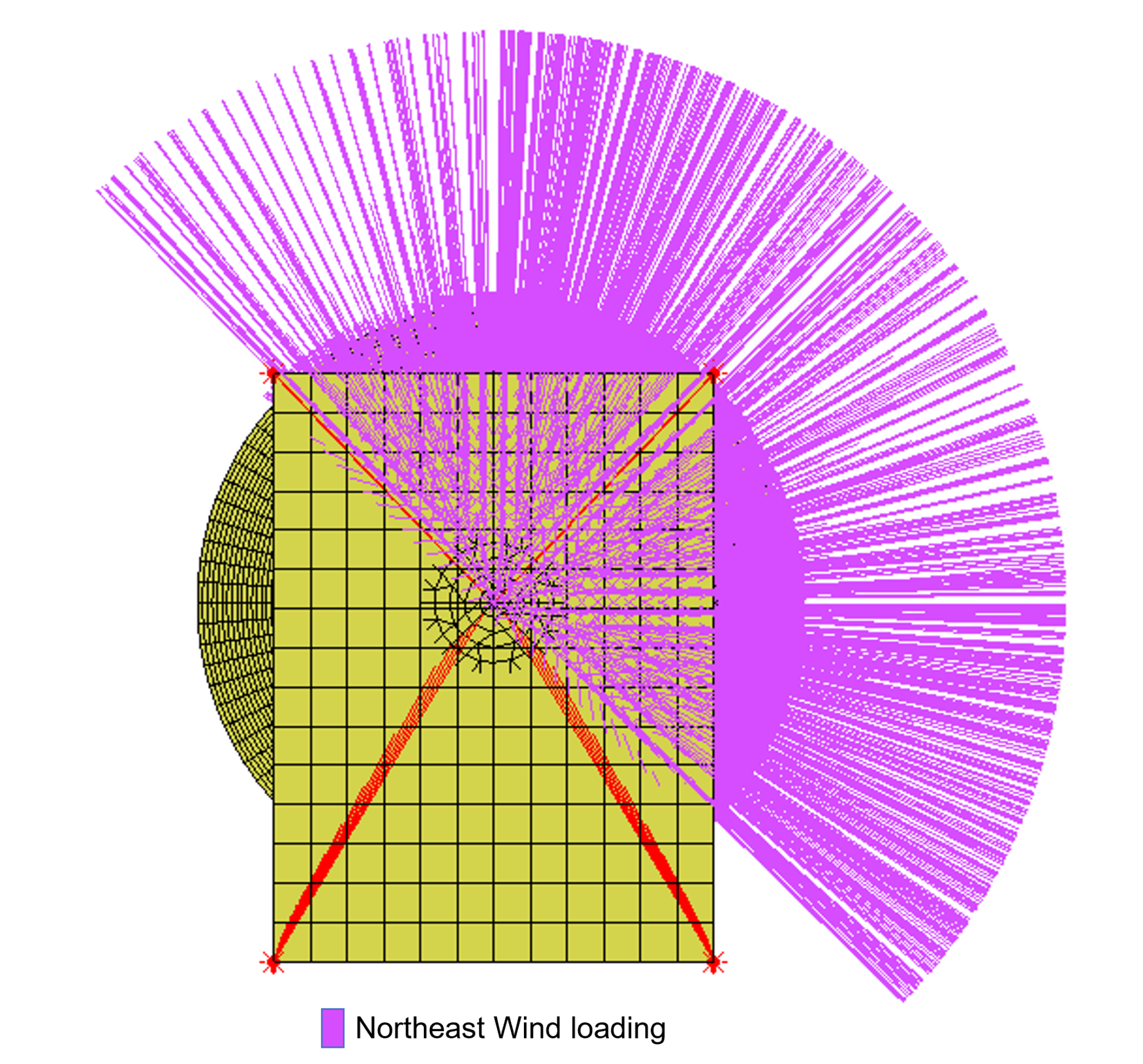
The DOCAN solution
PV Elite was used to quickly gain information on the vessel. Using all vessel characteristics and major attachments, a model was produced that provides information such as: code minimum thickness; wind loading per BS EN 1991-1-4; calculating the MDMT; and shell stresses considered under various load cases, such as wind loading or pressure only.
Maple mathematical software was utilized to produce formalized hand calculations for the wind loading pressures to be endured by the vessel, and the overturning moments that they will produce, as well as determining the thermal expansion of the vessel.
This provided verification of the results of the PV Elite model and allowed additional customization to consider all parameters and attachments that contribute to the wind loading effects. These Maple calculations give verification that the FEA models are constructed properly and giving sensible results that the client can understand and trust.
Various wind sensitivity studies were performed using MSC Marc, to determine the maximum cut-out size that can be removed at any one time and the most effective cut-out sequence to preserve the strength of the remaining vessel allowing the repairs to be contained within the allocated time for the client’s scheduled maintenance.
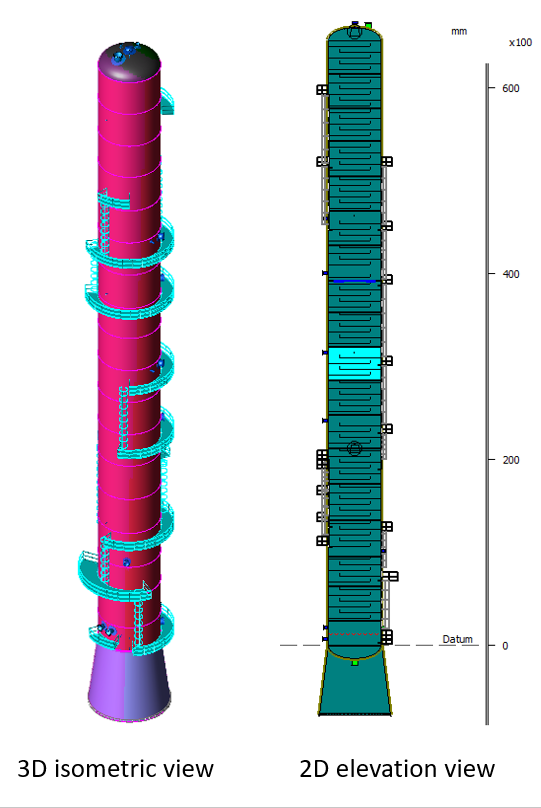
The outcome
Wind loads are produced to the requirements of the code that are used further in Finite Element Analysis to evaluate the response of the vessel in different configurations, such as mid repair with attached scaffolding. This was critical to predict whether unexpected weather may pose a substantial risk to the repair operation. This work allowed the timely and safe repairs of the required damage in the client’s vessel.
Project summary
Task | Application | DOCAN expertise | Pressure Vessels | Repairs | MSC APEX | MSC MARC | PV Elite | MAPLE | Wind loading |
---|---|---|---|---|---|---|---|---|---|
Proficiency in use of engineering standards | ASME VIII Div 1 | ![]() | ![]() | ![]() | ![]() | ![]() | ![]() | ![]() | ![]() |
ASME VIII Div 2 | ![]() | ![]() | ![]() | ![]() | ![]() | ![]() | ![]() | ![]() |
|
API 579 | ![]() | ![]() | ![]() | ![]() | ![]() | ![]() | ![]() | ![]() |
|
BS EN 1-4-1991 | ![]() | ![]() | ![]() | ![]() | ![]() | ![]() | ![]() | ![]() |
|
API 510 | ![]() | ![]() | ![]() | ![]() | ![]() | ![]() | ![]() | ![]() |
|
PCC-2 | ![]() | ![]() | ![]() | ![]() | ![]() | ![]() | ![]() | ![]() |
|
Engineering calculations | Wind pressure calculation | ![]() | ![]() | ![]() | ![]() | ![]() | ![]() | ![]() | ![]() |
Buckling analysis post-processing | ![]() | ![]() | ![]() | ![]() | ![]() | ![]() | ![]() | ![]() |
|
Pressure vessel modelling | Wind loading overturn moments | ![]() | ![]() | ![]() | ![]() | ![]() | ![]() | ![]() | ![]() |
MDMT | ![]() | ![]() | ![]() | ![]() | ![]() | ![]() | ![]() | ![]() |
|
Vessel design code check | ![]() | ![]() | ![]() | ![]() | ![]() | ![]() | ![]() | ![]() |
|
Minimum wall thickness | ![]() | ![]() | ![]() | ![]() | ![]() | ![]() | ![]() | ![]() |
|
Fitness For Service Assessment | Level 3 assessment | ![]() | ![]() | ![]() | ![]() | ![]() | ![]() | ![]() | ![]() |
Linear elastic analysis | ![]() | ![]() | ![]() | ![]() | ![]() | ![]() | ![]() | ![]() |
|
Non-linear elastic-plastic collapse | ![]() | ![]() | ![]() | ![]() | ![]() | ![]() | ![]() | ![]() |
|
Buckling analysis | ![]() | ![]() | ![]() | ![]() | ![]() | ![]() | ![]() | ![]() |