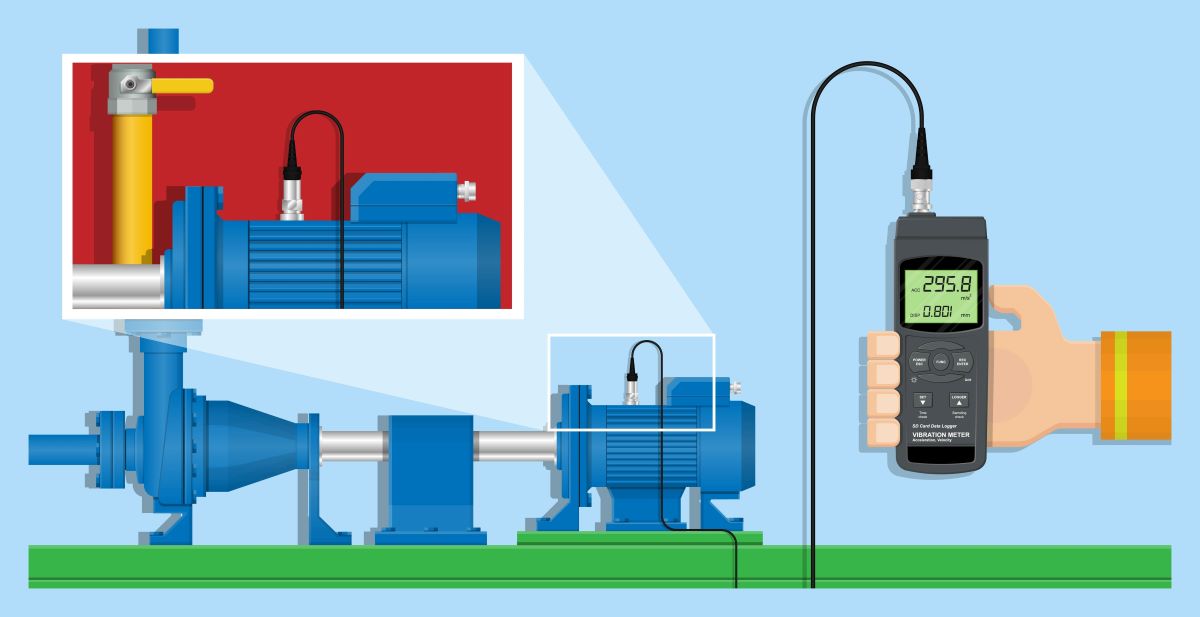
What is condition monitoring?
Condition monitoring is an indispensable tool for industries seeking reliability, efficiency and longevity in their operations.
Ever wondered how some industries manage to keep their equipment running like well-oiled machines (literally) at all times? Introducing, condition monitoring.
Condition monitoring is a practice that has become an indispensable tool for industries seeking reliability, efficiency and longevity in their operations. It can be considered a bit of a secret weapon and is often deployed in critical industrial applications such as oil and gas, nuclear and aerospace in addition to others.
This blog aims to introduce the concept of condition monitoring and how industries can utilise it to keep their machines operating optimally day in and day out, increasing uptime and reducing or removing unplanned failures.
Quick links:
Understanding condition monitoring
Condition monitoring is a method of either routinely or continuously monitoring the health and performance of machinery and equipment in real-time to detect any abnormalities, deviations or signs of deterioration. It’s essentially a surveillance tool that is designed to recognise any changes from the norm to alert any potential failures before they happen. This falls into the realm of predictive maintenance.
At the opposite end of the spectrum, we have preventive maintenance. This remains commonplace amongst manufacturing industries and relies on scheduling routine system check-ups and maintenance of equipment as per a recommended calendar date. However, this isn’t always efficient and can actually be counterproductive.
The reason behind this is that machines will typically signal their distress long before they fail, but this may not always be immediately obvious and can often result in a sudden breakdown before the next scheduled maintenance is due to take place. With condition monitoring, this kind of failure can be eliminated.
Condition monitoring involves the use of various sensors, instruments and technologies to gather data and analyse the state of the equipment whilst it’s in operation. The key components of condition monitoring include:
- Data collection: Sensors and instruments are used to collect data on parameters such as vibration, noise & acoustics, temperature, pressure, electrical currents, lubricant properties, and more, depending on the type of equipment being monitored.
- Data analysis: The collected data is analysed using various techniques and software to identify any trends, patterns and anomalies to help us assess the health and performance of the equipment.
- Reporting: Detailed reports represent the data in a visual format, allowing operators and engineers to make informed decisions regarding the equipment’s requirements.
- Predictive maintenance: From there, we can use this information to schedule maintenance and any repairs needed based on the actual health of the equipment, as opposed to adhering to fixed time intervals.
Why is condition monitoring important?
It’s probably clear by now that condition monitoring plays a crucial role across many industries to ensure the reliability, safety, and efficiency of equipment.
For companies who rely on machinery and equipment day in and day out, it’s not efficient to wait for them to break down and incur the costs that come with downtime. With the ability to monitor equipment in real-time, we’re able to solve the problem of unnecessary breakdowns and make informed proactive decisions to prevent equipment from getting to this point.
The core aim of condition monitoring is to maximise uptime and reliability which also optimises maintenance efforts, and is proven to be a far more efficient method than sticking to a rigid schedule. After all, there can be many causes of malfunctions such as user error or extreme operating conditions, which manufacturer-formed schedules can’t account for.
Advantages of condition monitoring
Some of the key benefits of carrying out condition monitoring include:
- Early fault detection – By routinely or continuously monitoring equipment in real-time, we can detect early signs of deterioration or any abnormalities before they escalate into more severe issues which helps to inform timely intervention and maintenance.
- Increased equipment reliability – Continuous equipment monitoring means that we can make sure all systems are operating within safe and optimal parameters, leading to increased reliability and reducing unexpected breakdowns.
- Predictive maintenance – Using the data collected, we can form predictive maintenance strategies that are informed by the actual condition and performance of the equipment. AI algorithms are now also available to help predictions.
Improved safety – Any potential safety hazards can be identified and addressed quickly, which is particularly important in critical applications. - Cost savings – Breakdowns, emergency repairs, expensive spare parts and production losses due to downtime can all be avoided with continuous condition monitoring. 6 to 12 months lost production due to availability of critical spares from a breakdown can be avoided.
- Extended equipment lifespan – Detecting faults before they escalate and organising proactive maintenance can contribute to extending the lifespan of equipment and reducing the frequency of costly replacements. The bathtub curve now becomes a lot longer.
Condition monitoring techniques
There are many different methods of condition monitoring that can be used depending on the type of equipment being monitored and the specific parameters that need to be measured.
The four main conditioning monitoring techniques are:
AE or Acoustic Emission
Acoustic Emission is a modern and cutting-edge technique which essentially is used to listen to the machine and is particularly useful for indicating very early when damage is being created, potentially well before vibration analysis will pick this up.
Vibration analysis
Vibration analysis is one of the most well-known and widely employed methods of condition monitoring across various industries such as oil and gas, power generation and manufacturing.
As the name suggests, this method involves monitoring and analysing the vibrations generated by equipment, using sensors to measure and record vibration levels and frequencies. These vibrations are then analysed to determine the condition and performance of the equipment to get a gauge of how healthy the system and its components are.
How to measure vibration frequency
An accelerometer is attached to the machine to measure how many times per minute or second the vibration occurs. This data is then analysed by engineers who can identify if there are any possible problems such as imbalances, motor faults, speed issues or anything else.
For example, if abnormal vibrations are indicated on a water pump whilst it is in operation this could indicate that a component is misaligned or loose and is therefore worth investigating.
Now, vibrations are to be expected whilst a piece of machinery is running which is why accurate vibration analysis is key to figuring out if this is within the normal range or not. Being able to accurately measure and analyse the results is key to a successful operation, which is why here at DOCAN we’ve heavily invested in our vibration-related services.
We’ve recently become the UK, Northern Ireland and Republic of Ireland representatives as well as corporate members of the Vibration Institute which supports us in offering industry best practices for cutting-edge solutions related to vibration. As an engineering consultancy that works within highly regulated industries, it’s critical that we employ methods of the highest standards and accuracy that add value to our clients’ projects.
Vibration Amplification
Vibration Amplification or VA is a method where high definition and high-speed video is taken of a machine, and post-processing of this footage is then used to amplify the magnitude of vibration and slow down the vibration, so it can be visually seen.
In some ways, this is analogous to having thousands of vibration sensors. For instance, out-of-balance, soft foot, and harmonic vibrations are simple to identify, and in many cases, the solution is visually obvious.
Thermography
Another way of monitoring the performance of equipment is to study the heat and radiation patterns within machinery, using thermography.
This method involves using infrared imaging to assess temperature and thermal patterns which can help to detect any anomalies or issues related to heat. As temperature variations within machines aren’t visible to the naked eye, thermography equipment is critical for identifying excessive temperatures from overload, bad cooling, electrical problems, poor lubrication, near end of life or over loaded bearings.
When thermal indications are seen on rotating equipment, end of life is imminent and is an indicator of severe damage.
Lubricant analysis
Also known as oil condition monitoring, this method applies to machine oils, fluids and lubricants and can detect any signs of contamination, overheating or wear and tear.
Numerous methods can be used but essentially, the purpose of analysing lubricants is to ensure they are effectively protecting and lubricating machine components. This type of analysis can provide valuable information about the condition of equipment – for example, if a high level of metal particles are discovered in the fluid, it’s a key indicator of wear in the system. Similarly, large amounts of water may indicate failed seals or low viscosity, and high flash point may indicate process fluids mixing into lube oil.
Adequate lubrication is the main contributor to the efficient and effective operation of many machines, and contamination or component wear is typically difficult to identify without accurate and continuous lubricant analysis.
DOCAN’s condition monitoring solutions
Here at DOCAN, we’ve helped many clients improve the efficiency of their operations through effective condition monitoring and solving their vibration issues. Check out how we recently assessed a turbine.
We’re uniquely positioned to be able to incorporate some of our many other advanced engineering skills within these projects, such as Finite Element Analysis, to add greater value and improve the accuracy of results.
If you have any equipment in need of condition monitoring, we can provide a range of different services including training, measurements and consulting. Get in touch with us to find out more.