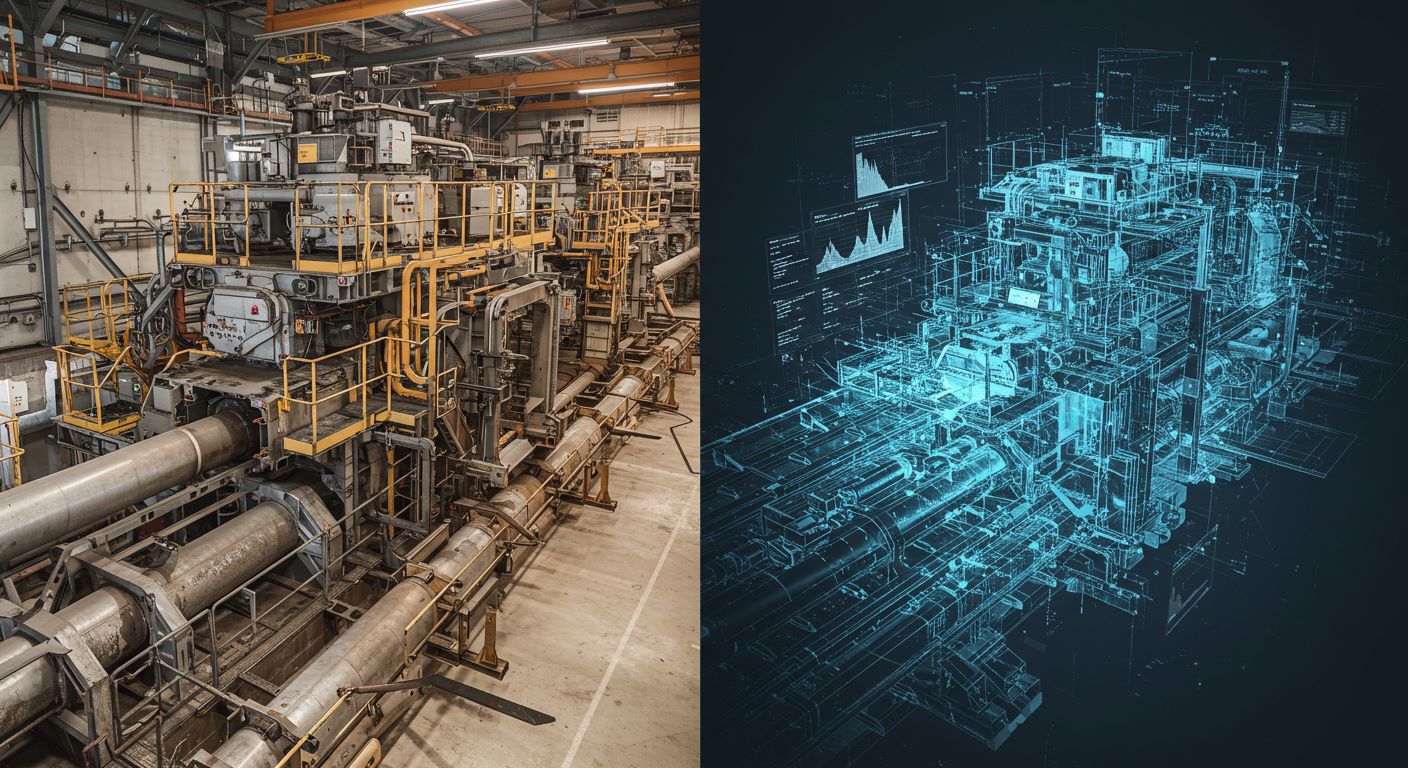
What is digital twin technology? Benefits & applications
Digital twin technology is an indespensable tool often used in many engineering projects.
Digital twin technology is an important tool that transforms the way we can manage, analyse and optimise assets. It’s more than a 3D model – it’s a highly accurate virtual representation of a physical system that allows us to simulate, test, and refine designs without needing direct access to the physical asset.
At DOCAN, we specialise in digital twin services, using cutting-edge 3D laser scanning, engineering software, and expert analysis to create digital twins that support everything from reverse engineering to Fitness for Service (FFS) assessments and more. But what exactly is a digital twin, and why is it such a game-changer for so many engineering projects?
Quick links:
What is a digital twin?
A digital twin is a precise digital replica of a physical object, system, or structure. From pipelines and pressure vessels to wind turbines and infrastructure, digital twins are applicable to many different assets and are a vital tool across industries such as oil & gas, energy, manufacturing and many more.
Digital twins go beyond a static 3D model by integrating real-world data that transforms it into a dynamic tool – we’ll discuss more on the type of data used later. Not only is the replica initially created using real-world data, but it means it can also be continually updated as the data changes, making it more powerful than a traditional CAD model.
For example, we can create a digital twin of a wind turbine that will simulate performance under different operating conditions, allowing for improvements in efficiency and early fault detection. (It is different to simulation though, which again we’ll cover later).
Similarly, we might develop a digital twin of an offshore platform to accurately monitor its structural integrity, assess corrosion levels, and predict maintenance needs before failures occur.
The list is endless, but hopefully, that clears up what a digital twin actually is and why we use them in many engineering projects.
How digital twins are created
At DOCAN, we take a comprehensive, in-house approach to digital twin development. Our process ensures maximum accuracy and efficiency:
- On-site measurement – We use state-of-the-art equipment such as the Leica RTC360, P40 long-range scanner, and Total Station to capture precise data from physical assets.
- Post-processing – The raw scan data is refined and structured into a global model, ensuring all details are accurately captured.
- Data integration – The processed data is exported into CAD systems, where it can be analysed and used for further engineering work.
- Project foundation – The digital twin serves as the foundation for a range of engineering tasks, from design modifications to reverse engineering and condition monitoring.
As mentioned above, it’s important that digital twins are based on real-world data so that we can closely mirror their real-world counterparts to get them as accurate as possible. This data may include the following:
- Sensor data: Live or historical information from IoT sensors, such as temperature, pressure, vibration, or strain measurements
- Operational data: Performance metrics, maintenance records, and usage history of the asset
- Environmental data: External factors like weather conditions, humidity, or load variations that affect the system
- Geospatial data: Positioning and dimensional accuracy captured through 3D laser scanning or GPS tracking
The way we collect this data at DOCAN is levels above what other companies may offer, as we do everything in-house. With access to 3D laser scanning technology, we collect all of the data ourselves which comes with its own range of benefits.
Firstly, we know exactly what we’re looking for so we don’t need to relay this information to an external company or our client, and risk any miscommunication or data being missed. Secondly, it means that our clients don’t have to invest in expensive equipment or software and above all else, it means we can ensure complete accuracy and precision as everything is under our control.
Digital twin vs simulation
At this point in the blog, digital twins might sound a lot like simulations which are another method we use to analyse and predict how systems behave. However, whilst they might have some similarities, there are a few key differences that set them apart.
The main difference between the two is that digital twins use real-time data, whereas simulations use theoretical data. To put this in simpler terms, digital twins can monitor the performance of an asset in real time and can replicate what is happening, whereas simulations predict what could happen in certain scenarios. However, they both have their place.
We would typically use a simulation when we want to model a specific scenario or process, entering predefined conditions to test specific conditions. This is crucial for when we’re testing specific conditions such as stress analysis or fluid dynamics and need to understand the impact that it may have.
Digital twins are the most suitable method when the project requires studying multiple processes because we’re able to monitor the behaviour of the system (or an exact digital replica of it) in real time. This means we can make informed decisions about system optimisation, track wear and tear, predict failures and continuously improve system performance.
Benefits of a digital twin
Digital twin technology is all about making highly informed data-driven decisions that improve efficiency, reduce costs, and enhance performance. Ultimately it helps to:
1. Improve decision-making
One of the fundamental features of a digital twin model is that it continuously updates to reflect real-world conditions. This means that we can accurately monitor real-time performance and identify any potential issues before they cause failures.
It’s not just about preventing issues though, we can also use it to make educated decisions on optimising operations to make sure everything is running as smoothly and efficiently as possible.
2. Save costs & reduce downtime
Having the power to simulate changes in a virtual environment reduces the need for physical testing, which can be substantially costly when you take into account the need to create a physical replica of the asset. In the same way, it means that we can minimise potential costly downtime by being able to identify and fix problems before they arise.
3. Enhance accuracy
In engineering, there’s no room for guesswork and much of what we do relies on precise, accurate designs that can withstand changes in loads or conditions. By using digital twins, we can make sure that designs are 100% accurate by performing better structural analysis and fitness-for-service assessments, ensuring fewer errors.
Key applications of digital twin technology in engineering
The capabilities of digital twins are nearly limitless and they’ve become a vital part of many different engineering processes for a range of industries and applications.
Once a digital twin has been created, it can be used across various engineering disciplines including:
- Reverse engineering: If the original design data of an asset or system is unavailable, we can use digital twin technology to recreate a component or structure with extreme accuracy.
- Fitness for Services (FFS) Assessments: We can use digital twin models to evaluate safety and structural integrity in a virtual environment before making real-world decisions.
- New design & system optimisation: Digital twins can be used to accurately test modifications, improve efficiency, and prevent design flaws before they are implemented on the physical product or system.
- Predictive maintenance & condition monitoring: As we create digital twins using real-time data, they can help to accurately predict failures so that proactive maintenance can be scheduled to prevent any downtime.
On the subject of condition monitoring, this is also an area in which DOCAN work with clients to ensure the efficiency and effectiveness of their processes. In combination with digital twin technology, we can help clients analyse and address any issues found as part of their condition monitoring strategies to ensure their systems continue to function efficiently over the long term.
How our digital twin services can help your project
DOCAN has a multidisciplinary team of skilled engineers with digital twinning capabilities, working across all major industries. If you have the requirements for a digital twin, we can help. Don’t just take our word for it though, here’s how we recently helped a client…
In a recent project involving a fire-damaged biodiesel storage tank, we utilised digital twin technology to conduct a comprehensive Fitness for Service (FFS) assessment. The tank had suffered significant shell distortion and weld ruptures due to the fire, raising concerns about its structural integrity. By creating a precise digital replica of the tank, we were able to simulate various stress scenarios and assess the extent of the damage without direct physical interaction. This approach allowed us to determine the tank’s suitability for continued use and to develop a targeted repair strategy. Click here to read the full case study.