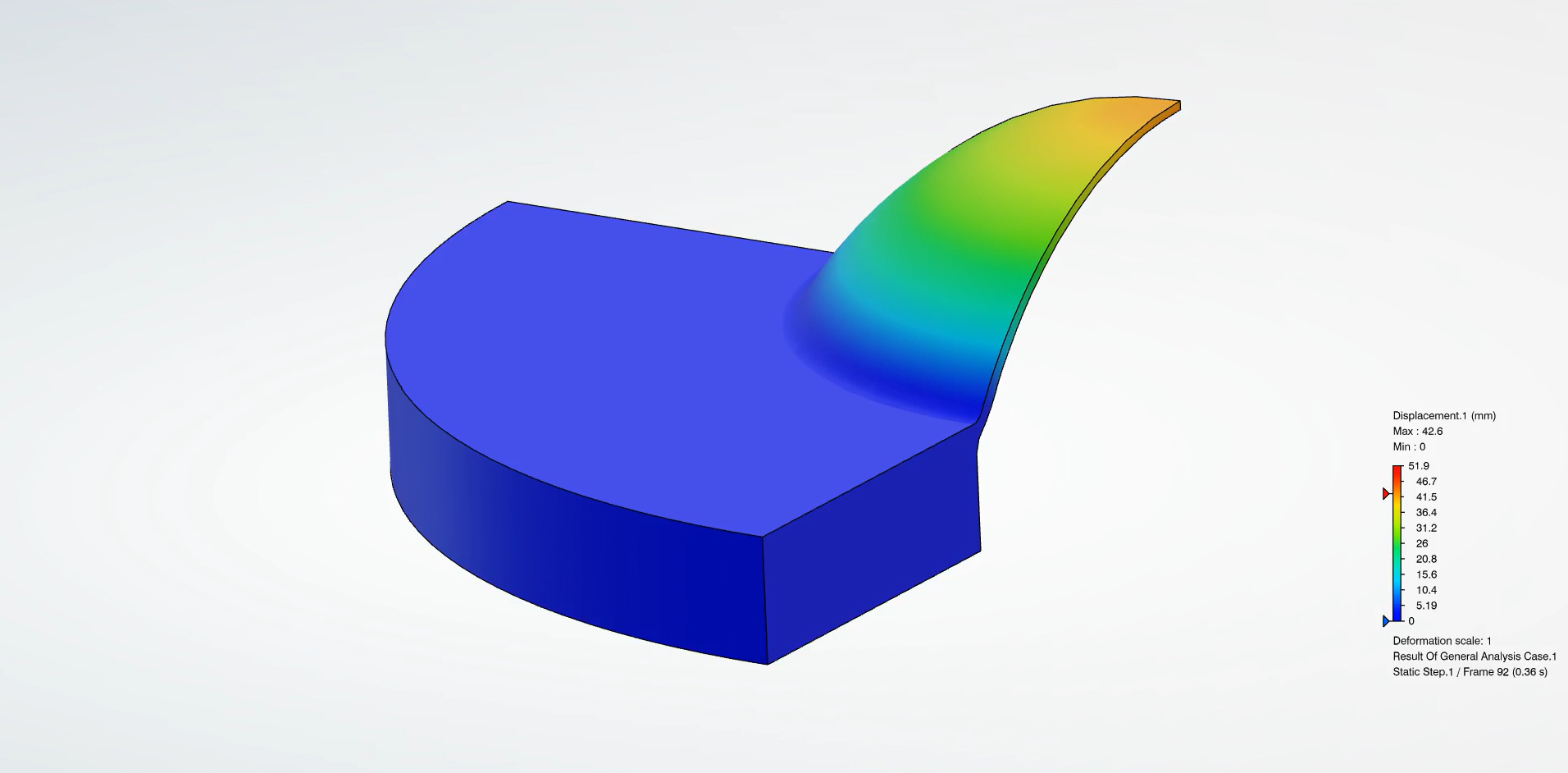
Benchmarking bursting disks in Dassault Systemes 3D Experience
Find out how one of our mechanical engineers used ABAQUS FEA to produce a benchmark simulation of bursting discs.
DOCAN has recently started trialling the 3D Experience platform for our FEA activities. But before we employ a new software package on safety-critical projects, we like to conduct benchmarking activities to understand that the software is giving us the answer we expect.
One of our mechanical engineers has produced a benchmark simulation of bursting discs as part of his training to understand the plastic failure of parts and methods of pressure system protection.
This benchmark is based on an old analysis example using ABAQUS FEA, and the benchmark itself has been run in the 3D Experience simulation software.
Read on for a detailed overview of the benchmarking process, and watch the simulation in action at the bottom of this article.
What are bursting discs?
Bursting discs or rupture discs are common components in pressure systems across a variety of industries. They are sacrificial safety valves, designed to reliably burst at a specified pressure to relieve the system in the event of an upset condition.
Forward-acting bursting discs burst like a balloon above their bursting pressure, failing in tension. Reverse-acting bursting discs have a more reliable bursting pressure, since they rely on elastic buckling as their failure mechanism. However for the purposes of this exercise, we will consider a forward-acting disc to avoid modelling buckling.
Quantifying bursting discs with FEA
There are several properties of a bursting disc we might like to calculate:
1. Allowable pressure: the pressure the bursting disc can operate at without sustaining damage
2. Failure pressure: the pressure at which the disc will rupture
Of course, one would normally refer to manufacturer specifications for off-the-shelf parts rather than resorting to simulations. We chose to build a 3D quarter model to test a range of functionality in this package.
Allowable pressure
To determine the allowable pressure, we used a combination of Simulia’s Stress Linearisation tool to extract classified stresses through various parts of the disk, in addition to running a fully non-linear elastic-plastic collapse analysis. Both of these methodologies follow the typical Design By Analysis methods given in the ASME Boiler and Pressure Vessel Code.
Failure pressure
From the analysis, we were able to determine the pressure at which the disk failed. The actual response that would be expected from the disk is shown in the image below, where the effect of very large deformations and plastic strains can be seen as the disk bulges under the action of the applied pressure.
Verdict
This benchmarking simulation is one example of how we can use the tools available within the 3D Experience platform in the field of pressure systems engineering, to design and assess parts and systems. Some of the functionalities of the software used here include stress linearisation, material plasticity and large deformation effects.
DOCAN are an approved sales partner for Dassault Systemes 3D Experience platform, and can offer bespoke training on the software to meet your needs and help you to utilise its tools to their full potential.
If you’d like to learn more about the software or make a sales enquiry, please get in touch with us online or call us on 01606 212330.