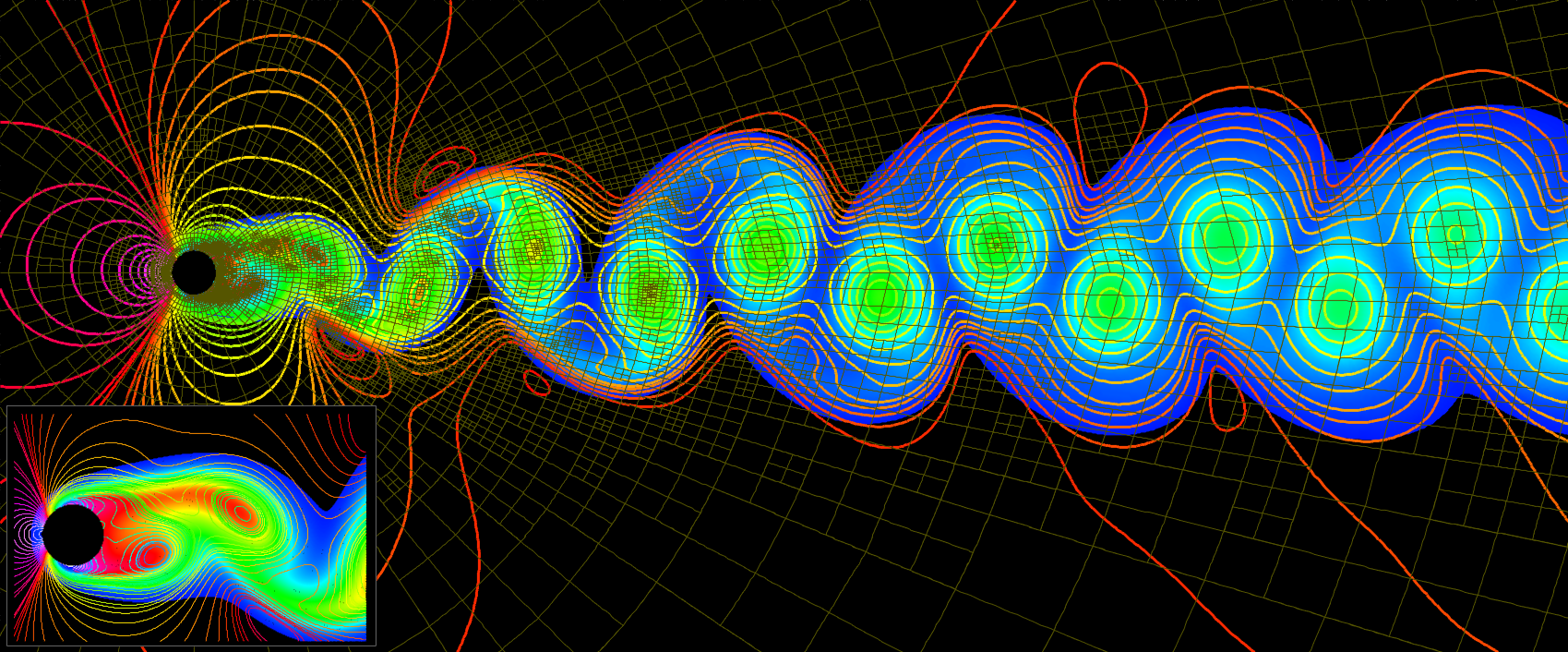
What is fluid dynamics?
An insight into fluid dynamics as a practice, with particular emphasis on its application within engineering.
Fluid dynamics is a subdiscipline of fluid mechanics, which in turn is the area of physics concerned covering the flow of fluids in both the liquid and gas state, as well as the forces on them. The overarching question is – how would a fluid behave relative to its state, the environment it is in and the forces exerted upon it?
The application of fluid dynamics is very broad. Fluid dynamics can be applied on the grandest of scales when it comes to geographical applications such as ocean currents and weather systems, but there are also technological, often intricate use cases within engineering – the prime example being an oil pipeline.
Using fluid dynamics we are able to assess fluid flow, predict flow parameters, analyse acoustic responses and predict structural fatigue amongst other uses.
The purpose of this blog is to give an insight into fluid dynamics as a practice, with particular emphasis on its application within engineering. It is produced for the general reader looking to educate themselves on the subdiscipline.
This blog will cover:
First of all, let’s define ‘flow’ in fluid dynamics
Simply put, ‘flow’ is the term given to the movement of liquid and gas. It’s important that we define this as we begin this blog post because fluid dynamics is entirely concerned with flow, by nature. How will a fluid behave based on its surrounding environment? Technically speaking there are two answers: steady, or unsteady – and in engineering, the fluid dynamics discipline is entirely concerned with diagnosing this in the process of creating improved flow.
Let’s take an oil pipeline as an example. Designed and built correctly, oil will flow through the system steadily, meaning that it is moving at a constant and uninterrupted rate. Interruptions to this rate of flow, such as a surge of oil through the pipeline, are unsteady.
Then, there’s the difference between laminar and turbulent flows. Laminar flows are smoother and turbulent flows are more chaotic. There are several reasons for either, but a crucial factor is the fluid’s viscosity. Again, if we take oil as an example, as a more viscous fluid there is more of a tendency for laminar flow. Whereas water would have much more scope to be turbulent. Just imagine if the entire Pacific Ocean was oil, tides would move in and out at a much slower rate.
Where is fluid dynamics used?
Fluid dynamics is prevalent throughout engineering disciplines, including hydraulic, aeronautical and chemical engineering and computation fluid dynamics (CFD) is an engineering tool used to simulate the behaviour of thermo-fluids in a system.
Aerospace
Fluid dynamics can be used to measure the forces acting on an aircraft. It allows an aerodynamicist to gain a more detailed understanding of a flow field around the craft, as well as a wide range of other analyses.
Hydraulic machines
Fluid is a critical part of all hydraulic machines, as fluid pressure is used to drive rams, pistons, and actuators. This allows the machinery to lift extreme loads or exert high pressure.
Thermal Power Plants
Water is used in thermal power plants, it is heated to generate steam that is passed into the blades of a turbine – thus producing electricity. Fluid dynamics work is required to assess and analyse the behaviour of the steam, as well as the recuperation of the water from the cooling component. There are similar procedures in nuclear plants.
How DOCAN can help
DOCAN have the tools and expertise to simulate a wide range of thermo-fluid engineering problems. Using co-simulation within our suite of software, effective Fluid Structure Interactions (or FSI) can be simulated, where the response of a structure to the fluid flow has an impact on the fluid flow until an equilibrium state is met, whether that is steady-state or oscillatory.
Global network models and full 3D CFD can be used to represent complex fluid flow, where characteristics of a piece of equipment are required for inputs, or the wind load imparted on an entire building. We use cutting edge CFD software which offers a series of practical, state-of-the-art CFD simulation and visualization tools, and our CFD tools can incorporate Multiphysics cosimulation to achieve couplings with Structural, Acoustic, Electromagnetic, Mechanical, OneDimensional, Optimization, Thermal Environment, 3D CAD and other relative analysis tools, to improve the accuracy of the simulations.
With our CFD software, we can model effects such as cavitation, aeroelasticity and erosion whether that pertains to equipment, buildings or land. This can be applied to model full HVAC responses, hydroelectric facilities, or piping networks.
Read a case study: Piping Slug Flow Simulation