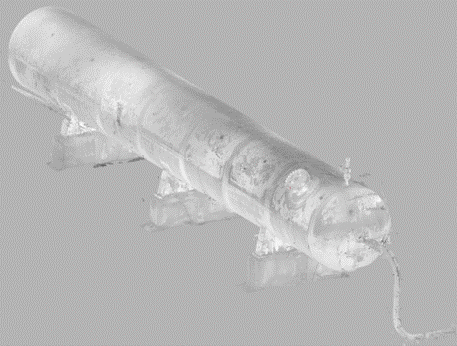
Measurement techniques for reverse engineering
An insight into how objects and materials are measured and analysed in the reverse engineering process, and how this data is then put to use to effectively reverse engineer a product.
Reverse engineering helps us to recreate and understand complex structures, systems or products. By inspecting, measuring, and possibly dissecting these systems and structures, we can gain invaluable insight and knowledge into the way they’ve been made and how they work.
We can apply reverse engineering to almost any product and there are various reasons for doing so, which we’ve covered in one of our previous posts: What is reverse engineering?
For the purpose of today’s article, we’re going to dive a little deeper into the process of reverse engineering and the techniques that can be used to analyse a product and recover its design, materials, requirement specifications and functions.
Quick links:
Traditional measurement techniques in reverse engineering
Traditional measurement techniques have been instrumental to the process of reverse engineering for many years, and they typically involve using manual tools and methods to gather accurate data and measurements.
Whilst more modern techniques have been developed such as laser scanning (more on that later), these techniques still prove invaluable in many cases for capturing the physical dimensions and characteristics of the product. These techniques cover the measurement of large-scale items (such as buildings) down to relatively small-scale items (such as small mechanical components).
Total stations – Large scale
Total stations are electronic theodolite devices that are equipped with integrated electronic distance measurement (EDM) capabilities which can measure angles and distances simultaneously.
The more widespread use of total stations is typically done by land surveyors and civil engineers to survey land and building constructions, but they also play a significant role in reverse engineering practices.
Through the process of measuring angles and distances, they can accurately capture spatial data which helps to create accurate 2D and 3D representations of objects. This is particularly useful when we’re working on reverse engineering objects that have more complex shapes, intricate details, and surfaces that are difficult to measure using alternative methods. Using the precise measurements gathered, we’re able to recreate the object digitally and analyse it.
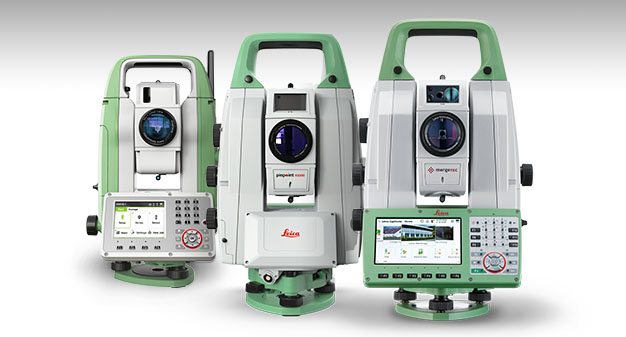
Leica total stations
Photogrammetry – Large scale
As the name may suggest, photogrammetry is a technique that uses photographs to measure and create 3D models of objects. The method involves capturing multiple images of the object from different angles, using a high-resolution sensor to ensure detailed and clear images. Generally, the more images taken from different viewpoints, the more accurate the 3D model will be.
Photogrammetry software is then used to process the images to calculate distances and dimensions. This method is incredibly useful for objects with intricate shapes and fine details and allows us to match common features, generate point clouds, generate mesh, and map textures.
We can also import the photogrammetric model into CAD software to be used as the basis for creating a parametric model in projects where the goal is to create a CAD model for manufacturing.
Coordinate Measuring Machines (CMM) – Small scale
CMMs are precision instruments used for accurately measuring the dimensions and geometric features of an object. They offer a high degree of accuracy and precision, making them ideal for reverse engineering applications that require detailed measurements, especially if the object is particularly complex.
They can be equipped with a probing system to gather data points from the surface of an object. Some may also have automated scanning capabilities which allow the probing system to move along the surface, capturing a continuous stream of data points.
Once the data points have been captured, the machine’s software will process them to create a point cloud or accurate 3D model. Through this, we’re then able to create surface meshes and analyse the digital model against the physical object in order to identify any deviations or inaccuracies.
3D laser scanning for reverse engineering – Large & small scale
Looking into the more modern measurement techniques used in reverse engineering, 3D laser scanning is one of the most common methods used today.
It’s a highly advanced and effective technology that’s used to capture detailed and accurate measurements of existing objects or structures. Laser scanners employ laser beams that capture millions of data points from the object’s surface in order to create a highly accurate and comprehensive 3D digital model.
The laser beams bounce off the object’s surface and return to the scanner, creating a dense cloud of points that represent the object’s geometry. We can then use this 3D model for analysis and recreation, modifying the design where necessary.
In comparison to alternative techniques, 3D laser scanning technology is favoured for its speed, accuracy, and ability to capture complex geometries and detailed surface features. Whilst the more manual and traditional methods certainly have their place, 3D laser scanning helps to reduce the time and effort required for reverse engineering projects as it streamlines the process and eliminates human error from manual calculations and interpretation of results.
Where the subject is a large-scale architectural structure or a particularly intricate object, 3D laser scanning would typically be employed as the main technique in order to enhance accuracy and speed up the process. It can also be used for individual components, as we did for a client who required manufacturing drawings for component reproduction.
Material identification techniques
A crucial step of the reverse engineering process is material identification, whereby we must determine the composition, properties and characteristics of the material used. This must be done whether we plan to replicate or improve the product so that we can get a deep understanding of the material’s behaviour, performance and suitability for the application.
This can be performed in different ways. Some of the main material identification techniques used in reverse engineering are:
Material hardness testing
Determining the hardness of a material is particularly important when we’re looking to replicate a product or its components, as we need to measure its resistance to deformation, indentation, or scratching.
By incorporating hardness testing we can better understand the mechanical properties of a material such as its strength, durability and wear resistance. Two specific methods that can be used here are scratch testing and indentation testing.
- Scratch testing – This typically involves dragging a sharp indenter across the material’s surface under a specific load, and measuring the depth of the scratch created. This can then indicate the material’s hardness and ability to withstand abrasion.
- Indentation testing – This is a similar method which involves applying a controlled force to an indenter which penetrates into the surface of the material. Again, the depth of this penetration will provide an insight into the material’s hardness and ability to withstand deformation.
Ultrasonic thickness measurement (UTM)
Ultrasonic thickness measurement (UTM) is a non-destructive testing method used to determine the thickness of a material’s cross-section.
To prevent any damage to the object, UTM uses ultrasonic waves which travel through materials. When applying this technique to an object, the wave is sent through the surface of the object until it encounters a boundary (the back surface of the object). A portion of the wave will then bounce back to the surface and we measure the time this takes, from there we can calculate the thickness of the material.
In reverse engineering, UTM is highly valuable when it comes to trying to understand the dimensions and structural integrity of structures or components.
It can be used on various materials such as plastics, metals and composites, and is one of the main material identification techniques we used when reverse engineering a nitrogen pressure vessel for a client. As the brief was to produce an engineering documentation pack for the vessel, it was critical that the measurements were taken in a way that prevented it from being damaged or altered in any way.
Materials composition analysis
Along with the hardness and thickness of a material, we also need to measure its chemical and elemental composition. If we’re reverse engineering a product to recreate or modify it, it’s critical that we understand the specific properties which determine its performance and behaviour.
Materials composition analysis is conducted by obtaining a representative sample of the material, and undergoing various analyses using techniques such as X-ray fluorescence spectrometry (XRF) for elemental analysis, and optimal emission spectroscopy (OES) for chemical analysis.
There are many ways in which the composition of a material can be analysed, but typically all are non-destructive testing methods which ensure the object or component remains intact.
Utilising the collected data to reverse engineer a product
Taking measurements and collecting the data is just the first step of the reverse engineering process. The data builds the foundation for what we want to achieve, so the way it is used will depend on the scope and desired outcome of the individual project.
Whilst every project is different, some of the key ways in which this data could be used are:
1. Redesigning and manufacturing equipment
This is typically required when the original design information for a piece of equipment is no longer available, but the project calls for a redesign or manufacture of this equipment with improved features or modified specifications.
In this case, we’d use the 3D models created from any of the above analysis methods to replicate the existing equipment and build on it from there. This type of reverse engineering is key for legacy equipment or critical components where documentation may have been lost due to age or changes within the organisation.
2. Retrofit of new equipment into existing equipment
This involves upgrading or adding new components to existing machines or systems, but it’s crucial that these updates have to fit and integrate seamlessly.
With the accurate measurements and material compositions available from the first phase of the process, we’re able to design new parts that fit the existing geometry to ensure a smooth retrofit without needing to recreate the entire system.
3. Performance assessment of existing designs
Reverse engineering doesn’t always have to end with a new product or upgraded design. Sometimes, the case may be that equipment needs to undergo a performance assessment but the design information is unavailable.
The information we’ve gathered from analysing the equipment will provide insights into the behaviour of the object under different loads and identify stress points, weaknesses or areas of improvement. Therefore, we can make well-informed decisions on any maintenance, modifications or upgrades needed to enhance its performance and/or longevity.
4. Benchmarking new designs against existing ones
Reverse engineering can be used effectively to gain a competitive edge by providing insights into existing competitor designs or equipment.
By using the methods of reverse engineering to understand how competitors’ products are constructed and how they function, we can identify areas where they excel but also where improvements can be made. This can then inform decisions on creating an upgraded product that ticks all of the boxes.
Advantages and disadvantages of reverse engineering
Reverse engineering is a versatile and incredibly powerful tool when implemented effectively. It offers several advantages but as with anything, it can come with its disadvantages too.
Reverse engineering advantages
- Product improvement and innovation – Reverse engineering is pivotal to understanding how existing products or systems have been designed. Being able to access this level of data, engineers can identify strengths and weaknesses in what’s already in the market, enabling them to create improved versions or more innovative products.
- Cost savings – When redesigning parts, components or entire systems, creating from scratch can be a drain on budget and time. If this information can be made available through reverse engineering, it’s often much more cost-effective as it reduces development time and costs, and eliminates the need for trial and error – particularly when it involves complex or intricate structures.
- Enhancing compatibility between different systems – If you want to integrate a new part or component into a system, the best way of ensuring that it will be compatible is by reverse engineering the existing design to reduce the risk of any potential conflicts.
- Knowledge transfer – Engineers can gain invaluable knowledge when reverse engineering a system and understanding the intricacies of different designs which can be transferred across projects and teams.
Reverse engineering disadvantages
- Possible incomplete/inaccurate data – Whilst the techniques we’ve covered are highly accurate, stumbling blocks can arise particularly if not performed correctly. Therefore, it may not always provide a complete understanding of the original design which can lead to potential inaccuracies.
- Time-consuming – The process is complex and must be completed to a high level of accuracy, which can often have time constraints particularly when dealing with complex or intricate systems.
- Integration challenges – When using reverse engineering to design and integrate new parts into existing systems, there is always a risk of compatibility issues no matter how accurate the data may be.
- High skill requirement – The process requires a deep understanding and a high level of engineering knowledge to be performed correctly and produce accurate results. This means it can often be a challenge to access the right level of skill required for the project.
DOCAN’s reverse engineering services
Following on from our previous point, if a lack of skill is what’s putting your reverse engineering endeavours on hold, this is where we come in. We’re an experienced engineering consultancy with specialist skills in reverse engineering across many applications and industries.
We offer clients a full reverse engineering service with our expertise covering 3D scans, material hardness testing, design and verification of new parts and creating engineering drawings. If you think we can help with your project, get in touch with us.
Enjoy this article? You may be interested in some of our others: