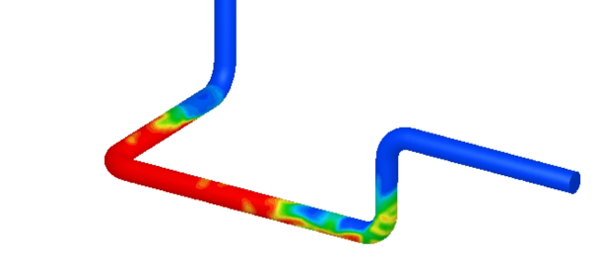
Solving fluid dynamics problems in pipes
When dealing with any fluid dynamics problem in a pipe, we can simulate and analyse it virtually through Computational Fluid Dynamics (CFD).
Fluid dynamics is a fascinating but complex engineering domain, but with an understanding of how it all works we can gain valuable insights into how liquids behave inside pipelines and solve or mitigate common problems such as pressure drops.
Here at DOCAN, we specialise in navigating the complexities of fluid flow using advanced simulation and analysis techniques to keep our client’s pipelines running smoothly and efficiently. In this blog, we’ll share our expertise on why fluid dynamics problems happen and how we can solve them.
We’ve used the example of fluid flow in pipes for discussion here, however, the subject of fluid dynamics covers many different applications across all industries with some real world examples given on our Projects page.
Quick links:
Understanding fluid dynamics in pipes
Before looking into some of the fluid dynamics problems found in pipes and how we can solve them, it’s worth covering some of the basic concepts surrounding fluid flow in pipes.
Fluid dynamics focuses on understanding how fluids behave when they’re in motion, and how they interact with their surroundings. So, this can include looking at the forces that affect fluid flow, the energy within the fluid, and how the fluid’s movement affects objects around it. By getting an understanding of these factors, we can solve problems relating to fluid flow in just about any piping system.
However, there are also two main types of fluid flow in pipes:
- Laminar flow: This is what we’d describe as a smooth, consistent flow where the fluid moves in orderly layers without disruption and minimal mixing. For example, oil typically travels through pipes with a laminar flow due to its high viscosity making it less likely to become turbulent and mix chaotically.
- Turbulent flow: On the other hand, turbulent flow is exactly as it says on the tin. Something like water will be fast-flowing and irregular due to its low viscosity and tendency to move in a zigzag fashion.
So, when we’re looking at fluid dynamics problems we first need to understand which flow we’re working with as that will affect how we analyse and solve them.
Common fluid dynamics problems in pipes
Having worked with many piping systems across various industries, we know they can present some interesting challenges. The intricacy and complexity of piping systems means they need to be properly managed, otherwise, fluid flow problems can creep up and that’s every business’s worst nightmare.
Fluid dynamics problems can lead to inefficiencies and damage to the system, which can have a knock-on effect on the overall operational performance. Downtime, safety hazards and costly repairs aren’t ideal, so it’s important to be aware of some of the most common problems we find in pipes.
Blockages and leaks
Blockages: No matter the set-up, equipment quality or maintenance schedule, pipes are susceptible to getting clogged up over time. Whether it’s debris, mineral deposits, or even growth like algae, any blockages in pipes can reduce the flow rate and cause pressure to build up behind the blockage, potentially leading to pipe bursts.
Leaks: Similarly, any cracks or holes in pipes can lead to leakages which can cause a whole host of problems. Not only is it wasting fluid, but leaks reduce the overall pressure and flow rate of the system as the fluid isn’t reaching its destination.
Pressure drops
When fluids move through pipes they lose pressure due to friction with the pipe walls and internal friction within the fluid – this is known as a pressure drop. If significant, it can greatly reduce the efficiency of the system as it requires the pump to work harder and consume more energy.
If we take a water distribution system for example, a pressure drop within the pipe can result in weak water flow from the tap when turned on.
Flow rate issues
In order to perform efficiently, piping systems need to maintain a consistent flow rate. If we start to see variations in flow rates this can disrupt processes, cause uneven heating or cooling, and reduce the system’s overall efficiency.
This can happen when the speed at which fluid moves through the pipes is inconsistent or insufficient which can be due to many things such as blockages, leaks, pump malfunctions or improper pipe sizing.
Multiphase flow, where liquid and gas mix and flow through a pipe, can lead to damaging flow regimes such as slug flow. This is one of the most damaging issues where fast-moving liquid slugs can cause structural issues in pipework.
Corrosion and erosion
Both are common occurrences in pipelines, particularly ones that have been operational for a long period of time.
Corrosion refers to the gradual degradation of pipe materials due to chemical reactions, often involving the transported fluid. Erosion, on the other hand, occurs when the fluid flow wears away the material of the pipe, especially at high velocities or with abrasive fluids.
Either of these issues may lead to leaks or bursts, impacting pressure and flow rates.
With so many reasons why a pipeline might be experiencing fluid flow problems and no two challenges being the same, it’s important to figure out the root cause before we can solve it.
Solving fluid dynamics with CFD
When dealing with any fluid dynamics problem, it’s not quite as simple as being able to take a look inside the pipe to see the fluid moving and identify exactly what the issue is. However, we can simulate and analyse it virtually through the power of Computational Fluid Dynamics (CFD).
We have a previous blog post explaining exactly what CFD is so we won’t go into too much detail here but essentially, it’s an advanced method that allows us to create virtual simulations of fluid flow. It uses both numerical methods and computer simulations to study fluid behaviour, analyse forces and pressures, and predict performance in a completely virtual environment.
Why do we use CFD to solve fluid flow problems?
CFD is an invaluable tool in diagnosing fluid flow problems as unlike traditional experimental methods, we can simulate and analyse fluid flows under various conditions without the need for physical prototypes or tests. These simulations give us a detailed and dynamic view of what’s happening inside a piping system without opening a valve or unscrewing a joint.
Not only does this save time and money, but we can get a deeper understanding of fluid dynamics phenomena that may be difficult to directly observe. For example, if we’re contacted by a client to diagnose a pipe flow problem in an oil rig, CFD is a safer, more efficient and less obtrusive method. And, it’s more accurate than any manual assessment could be.
CFD isn’t all about fixing current issues, it can help to prevent them too. Using CFD we can predict a number of things such as flow patterns, heat transfer, pressure and temperature distribution, and identify areas prone to corrosion. With these types of insights, we can advise on areas of optimisation so we can be proactive rather than reactive.
How to solve fluid flow problems with CFD
So, how do we actually perform a CFD analysis?
Having access to specialist CFD software is an essential part of this process. There are many different tools available, but typically we’ll look to using Ansys Fluent when solving any complex fluid flow problem.
In regards to the approach itself, this generally remains quite consistent however the exact process can vary depending on the specific problem and software being used. That being said, we can outline how we’d typically look to set up a CFD analysis to tackle fluid flow challenges.
1. Problem definition and geometry set-up
Before anything else, we want to clearly outline the goals of the simulation – this could be anything from optimising flow efficiency to reducing pressure drops or studying heat transfer.
Then, we’ll use CAD software to create a 3D model of the piping system or component. Here, we’ll need to define the dimensions, inlet/outlet locations, and any internal features like valves or bends.
2. Mesh generation
CFD meshing is a crucial pre-processing step where we divide a complex geometry into smaller, discrete elements called a mesh. This acts as a computational grid for solving fluid flow problems and directly impacts the accuracy of the simulation.
To create the mesh, we need to define boundary conditions such as fluid properties (density, viscosity), inlet velocity profiles, outlet pressures, and wall conditions (smooth, rough, insulated). The software will then generate the mesh depending on the boundaries set, and this can be refined if needed.
3. Defining numerical conditions
We also need to configure the numerical parameters, which include setting up solver options, choosing discretisation schemes, and other related settings.
Each type of simulation has its own specific requirements, and while multiple solvers and parameter combinations can be used to tackle a problem, selecting the appropriate ones is crucial for efficiency. Accurate solver parameters and numerical schemes are essential for solving the problem effectively and getting reliable results.
4. Running the simulation
At this stage, we’re ready to start the CFD solver which will simulate how the fluid flows within the defined area based on the rules of fluid dynamics, numerically solving the equations.
The simulation should be monitored to make sure it’s producing stable and accurate results. If things don’t look right, the solver settings can be tweaked until everything runs smoothly and correctly.
5. Interpreting the results
This is also known as the post-processing stage and is the final step in the CFD process. We need to analyse the simulation results using post-processing tools to visualise flow patterns, pressure distributions, contours etc. The interpretation of results allows us to identify areas of concern and evaluate system performance to better inform optimisation decisions.
While the above steps outline a general approach to solving fluid flow problems with CFD, the specific steps and details will vary depending on the problem’s complexity, the industry, and the software being used.
Of course, performing a CFD analysis takes a good understanding of the physics and system behaviour, requiring both technical knowledge and experience. The team at DOCAN have extensive experience applying advanced CFD methods to complex fluid flow problems across a wide range of industries. If you require assistance solving a fluid dynamics problem, please get in touch with us to find out how we can help.
Real-life examples of solving fluid dynamics problems
Understanding the theory and methodology is one thing, but how do we put it into practice and solve fluid dynamics problems with CFD? Let’s take a look at some of our work at DOCAN, to demonstrate real-life cases.
One of our clients contacted us after a steam line in a power generation system developed a circumferential crack. We were asked to evaluate the safety perimeter for the released high-pressure, high-temperature steam as it posed numerous health and safety risks.
Through CFD, we modelled the steam flow to define a precise exclusion zone based on temperature, velocity, volume, and pressure. This enabled our client to ensure worker safety and plan repairs while predicting potential risks associated with the crack’s expansion. Read the full case study.
We also recently used CFD to help a client in the food manufacturing industry who faced a complex design challenge requiring deep insights into fluid flow behaviour. We applied our engineering expertise in CFD methods, focusing on modelling non-Newtonian liquids, analysing pressure drops and velocity changes, and simulating mechanical systems such as sliding interference fits and large deformation effects.
This lasted over the course of several weeks and our iterative CFD simulations provided critical insights, meaning we could help them evaluate design impacts, guide further development, and avoid unnecessary physical testing. Read the full case study.
Need help solving a fluid dynamics problem?
Fluid dynamics is an incredibly advanced engineering domain, and without the right experience, expertise or tools, trying to navigate its complexities can lead to unreliable results.
DOCAN’s CFD consultants have a complete understanding of fluid behaviour, precise modelling techniques and accurate analytical tools enabling us to successfully tackle fluid dynamics challenges. We help clients where they don’t have this level of in-house skill or resources, working closely with them on their projects where they might need a little more help.
If it sounds like we could help with your project too, please get in touch with us.