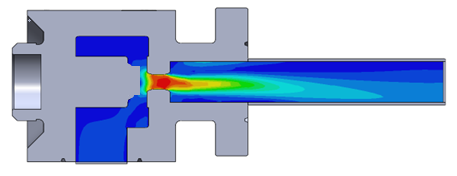
What is Computational Fluid Dynamics (CFD)?
A detailed insight into the practice of CFD analysis and why it's crucial to problem-solving in engineering.
Computational Fluid Dynamics (CFD) has revolutionised the way we design, analyse and optimise fluid-related processes.
By creating accurate digital simulations of products or systems, we can visualise the flow of fluids and how they’re affected by internal and external factors. From there, we can translate this into real-life situations and optimise the model to account for this change in behaviour.
It’s a complicated field of engineering, but incredibly useful for various reasons.
In this blog, we’ll explore what CFD is, the myriad of problems it can solve and why it’s become indispensable in engineering.
Quick links:
- What is CFD?
- How does CFD work?
- The role of CFD in engineering
- What problems can be solved with CFD?
- Can CFD help your project?
What is CFD?
CFD is a branch of fluid mechanics that employs various numerical methods and algorithms to solve and analyse problems related to fluid flow and heat transfer.
CFD allows us to simulate the behaviour of fluids and the forces acting on them to solve complex mathematical equations related to fluid, fluid-solid or fluid-gas interactions. It’s a powerful tool that we can use in the product development process by replicating operating conditions. We can accurately calculate and predict real-world physics and how the product will react in changing conditions, enabling us to optimise the product’s design and performance to ensure a more efficient final product.
It’s a multidisciplinary field of engineering that can be applied to many different industries and applications, for example solving aerodynamic problems within aerospace engineering, and understanding heat transfer within nuclear reactors.
How does CFD work?
Conducting CFD analysis is incredibly complex and comprises a series of stages involving intricate equations and problem-solving techniques. The primary equations used in CFD are the Navier-Stokes equations, which describe the conservation of momentum, mass and energy for a fluid.
Whilst there are many different aspects involving many different changing properties such as mass, heat and velocity, the process can be broken down into stages. Essentially, we can look at it as taking a huge problem and dissecting it into smaller, more manageable chunks.
Here’s a basic, simplified rundown of how CFD analysis works:
Geometry creation: When preparing a CFD simulation, we must first create a digital representation of the physical product, known as the geometry. The shape and boundaries of the fluid domain must be accurately defined, including any solid objects present. Using specialised software such as PowerFLOW CFD we can build an accurate real-life representation of the model to be analysed.
Mesh generation: The geometry is then divided into a grid of small elements or cells, known as the mesh. Depending on the complexity of the problem, this may be formed using structured or unstructured grids but either way, the quality of the mesh is crucial as it can significantly impact the accuracy and efficiency of the simulation.
Defining boundary conditions: Essential in CFD, boundary conditions specify how the fluid interacts with the domain’s boundaries. At this stage, we’ll set values for parameters like velocity, temperature, and pressure at the boundaries to ensure the conditions are mimicking the real-world environment. They are then translated into mathematical models ready for the solver.
Solving: Once the physics has been defined, the software’s solver will begin to solve the Navier-Stokes equations numerically. This can either be performed as transient, whereby the simulation will update at each step to capture changes in the fluid behaviour over time, or steady state to generate the results at equilibrium.
Post-processing and evaluation: Once the simulation is complete, we can then analyse the results by extracting the relevant data and interpreting the findings. At this stage, we can see graphical representations of the data which provide a detailed overview of the product’s behaviour.
Optimising the product: We can use the findings to optimise the product for efficiency and performance. The model will change with any updates made, providing instant feedback and allowing us to make continuous improvements and refinements with verification of the final solution.
Of course, this is a very basic overview of the CFD process and whilst advances in technology have helped to streamline and reduce the time taken to manually calculate fluid flow problems, an understanding of the CFD theory and Navier-Stokes equations is essential when ensuring complete accuracy in performing the analysis and interpreting the results.
The role of CFD in engineering
At its core, Computational Fluid Dynamics provides engineers with valuable insights into fluid behaviour, allowing us to make informed decisions and optimise product or system designs.
It plays a pivotal role in engineering for various reasons, including:
- Cost efficiency: CFD eliminates the need for traditional experimental methods for studying fluid dynamics, such as developing physical prototypes or undergoing wind tunnel testing, which can be expensive and time-consuming. Therefore, reducing costs in the product development process significantly.
- Quicker time to market: Rapid prototyping means we’re able to quickly iterate through different designs and scenarios, speeding up the product development process whilst exploring more design possibilities. This accelerates the whole development phase and usually means the product can be finalised sooner.
- Safety: Some fluid dynamics problems involve environments that are too harsh, remote or dangerous for direct experimentation, such as those within the nuclear space. Through CFD, we can study these environments virtually without putting lives at risk.
- Detailed insights: The insights gained about fluid behaviour, velocity, pressure, temperature and turbulence are invaluable and often unattainable through physical experimentation alone.
- Environmental considerations: CFD is paramount in the bid to design more eco-friendly solutions by optimising fluid processes for efficiency and reduced emissions.
- Research and innovation: It’s a powerful tool for those working on developing cutting-edge technologies, allowing engineers to explore unchartered territories and understand fluid dynamics in extreme conditions. The simulations contribute to developing innovative solutions due to gaining advanced scientific knowledge of fluid behaviour.
What problems can be solved with CFD?
It will come as no surprise that CFD is incredibly versatile and can be applied to a wide range of fluid flow problems across industries. Essentially, whenever there’s a requirement to make design decisions based on fluid problems, CFD can be implemented.
Widely used as a valid engineering tool, some of the most common types of problems that CFD can address include:
Aerodynamics
CFD plays a critical role in aerospace engineering, typically employed in the design of aircraft, rockets and drones. By understanding the lift, drag and stability characteristics of these vehicles we can optimise propulsion systems, wing shapes and control surfaces for increased efficiency, performance and safety.
Heat transfer
CFD can model heat transfer processes, including conduction, convection, and radiation, to ensure proper temperature control and heat dissipation. This is essential in many engineering applications, from designing efficient cooling systems to optimising the performance of nuclear reactors.
Fluid-Structure Interaction (FSI)
CFD can be used in conjunction with Finite Element Analysis to study fluid-structure interactions in cases where fluid flow interacts with solid structures. This can apply to the behaviour of underwater structures for example, and allows us to investigate the stresses and forces on structures due to fluid motion.
Environmental modelling
CFD can model and predict environmental phenomena such as air pollution dispersion, the behaviour of oil spills and water flow in oceans and rivers. This can help us to assess and mitigate the environmental impacts of such events.
Can CFD help your project?
If a project requires designing products or vehicles with enclosures where air or fluid flow is important, CFD will be an essential tool in optimising their design to ensure they perform to their full potential.
However, understanding the CFD process and calculations, and being equipped with the right tools are critical in ensuring accuracy. If you’re in a position where a CFD expert isn’t at your disposal, we’d recommend enlisting the help of an experienced CFD consultant.
DOCAN offers industry-leading Computational Fluid Dynamics consultancy services to solve complex fluid flow and heat transfer problems. We have vast experience applying state-of-the-art CFD methods and implementing cutting-edge CFD software and tools to improve the accuracy of the simulation.
We’ve helped many clients overcome their fluid flow problems, in industries from oil & gas and power generation to food production. If you think we can help with your project, get in touch with us.
Enjoy this article? You may be interested in some of our others: